Slag-pushing refining process under protection of inert gas
A technology of inert gas and slag topping, applied in the direction of improving process efficiency, etc., can solve the problems of not having the steps of slag washing and refining, and the unavoidable secondary oxidation of molten steel
- Summary
- Abstract
- Description
- Claims
- Application Information
AI Technical Summary
Problems solved by technology
Method used
Examples
Embodiment 1
[0018] 38 tons of HRB335 molten steel were smelted in a 40-ton converter. The molten steel enters the ladle after final deoxidation. Add slag adjusting agent to adjust the alkalinity of slag to 2.5 during the tapping process, and make the slag layer thickness about 50mm. Put the cover on the slag surface, and then fill the space between the cover and the slag surface with Ar. Make its lower edge close to the steel-slag interface. Add Al particles to the slag to make the (Feo) content in the slag 2.0%. Blow argon into the molten steel to fully mix the steel slag. The refining process was terminated after 10 minutes of argon blowing. The T[o] content in the steel before and after treatment was measured with an EMA620W analyzer, and the deoxidation efficiency was calculated to be 43%; the [S] content in the steel before and after treatment was analyzed, and the desulfurization efficiency was calculated to be 14.2%. The temperature during the treatment was reduced to 19°C.
PUM
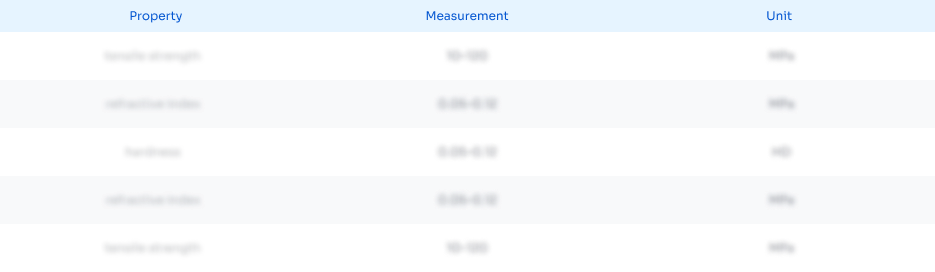
Abstract
Description
Claims
Application Information

- Generate Ideas
- Intellectual Property
- Life Sciences
- Materials
- Tech Scout
- Unparalleled Data Quality
- Higher Quality Content
- 60% Fewer Hallucinations
Browse by: Latest US Patents, China's latest patents, Technical Efficacy Thesaurus, Application Domain, Technology Topic, Popular Technical Reports.
© 2025 PatSnap. All rights reserved.Legal|Privacy policy|Modern Slavery Act Transparency Statement|Sitemap|About US| Contact US: help@patsnap.com