Method for controlling plate sizes of middle or thin plate planks in continuous casting and rolling processes
A medium-thin slab continuous casting and comprehensive control technology, which is applied in metal rolling and other directions, can solve the problem that the interference cannot be eliminated, the strip shape and thickness control cannot be fully coupled, and it is difficult to achieve flatness, convexity and edge drop Comprehensive control and other issues
- Summary
- Abstract
- Description
- Claims
- Application Information
AI Technical Summary
Problems solved by technology
Method used
Image
Examples
Embodiment Construction
[0071] Such as figure 1 Shown, the medium-thin slab continuous casting and rolling strip shape comprehensive control method of the present invention is characterized in that:
[0072] 1) Using new roll technology, through the roll shape design of the work roll and back-up roll of the finishing mill, the roll shape curve of the work roll and the back-up roll are processed by a CNC grinder. For the roll surface length of 1500mm to 2600mm, the diameter The roll shape of the working roll of 500mm-1100mm, that is, the diameter difference in the roll surface is 0-0.60mm, and the roll shape of the backup roll with the roll surface length of 1200mm-2300mm and the diameter of 1200mm-1600mm, that is, the diameter difference of the roll surface 0mm ~ 1.00mm.
[0073] 2) Calculate the bending force of the work roll and the position of the work roll through the secondary computer, and the control system designs and adjusts the bending force and the position of the work roll according to t...
PUM
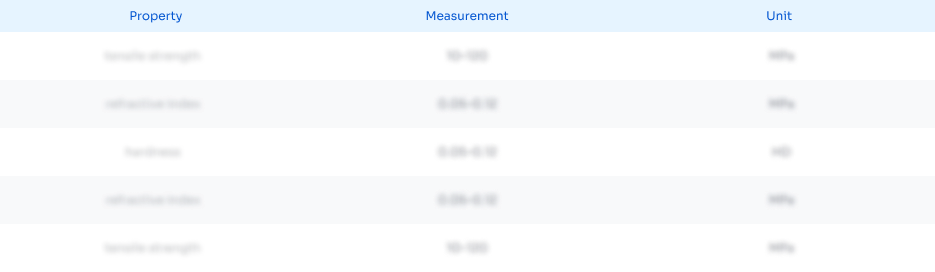
Abstract
Description
Claims
Application Information

- R&D
- Intellectual Property
- Life Sciences
- Materials
- Tech Scout
- Unparalleled Data Quality
- Higher Quality Content
- 60% Fewer Hallucinations
Browse by: Latest US Patents, China's latest patents, Technical Efficacy Thesaurus, Application Domain, Technology Topic, Popular Technical Reports.
© 2025 PatSnap. All rights reserved.Legal|Privacy policy|Modern Slavery Act Transparency Statement|Sitemap|About US| Contact US: help@patsnap.com