Undersensor magnetic suspension rotor system
A magnetic levitation rotor and sensor technology, used in bearings, shafts and bearings, control using feedback, etc., can solve problems such as extra noise, lubricating fluid pollution, wear, and excessive heat generation.
- Summary
- Abstract
- Description
- Claims
- Application Information
AI Technical Summary
Problems solved by technology
Method used
Image
Examples
Embodiment approach
[0021] The principle diagram of the rotor structure of the under-sensor magnetic levitation (hard disk structure 2) of the present invention is as follows Figure 5 As shown, it is the second embodiment of the present invention, the hard disk platter 1 is connected with the housing 7 by screws 2 .
[0022] Under-sensor magnetic levitation rotor system, including rotor 9, motor rotor 8, housing 7, motor stator 6, A / D, DSP, D / A and its power amplifier, housing 7 is equipped with motor stator 6, sensor bracket 11 and 2 A tapered magnetic bearing stator 4; the rotor 9 is covered with two conical disks 10, and the two tapered magnetic bearing stators 4 are respectively located above and below the rotor 9; the sensor bracket 11 is located between the two tapered magnetic bearing stators 4, and the sensor bracket 11 is installed There are 4 sensors 5, denoted by S 1 , S 2 , S 3 , S 4 Indicates that the sensor S 1 , S 2 Arranged in a conical surface, the sensor S 3 , S 4 Arran...
PUM
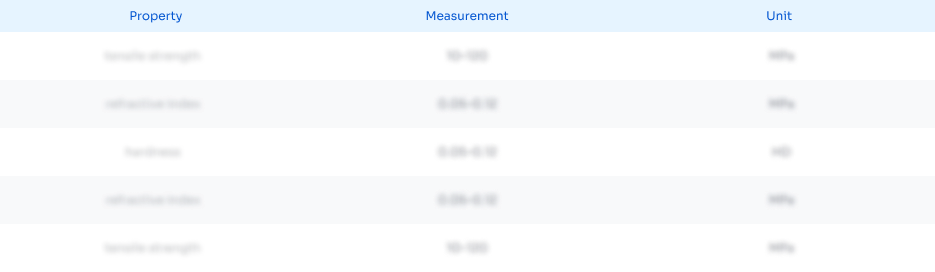
Abstract
Description
Claims
Application Information

- R&D Engineer
- R&D Manager
- IP Professional
- Industry Leading Data Capabilities
- Powerful AI technology
- Patent DNA Extraction
Browse by: Latest US Patents, China's latest patents, Technical Efficacy Thesaurus, Application Domain, Technology Topic, Popular Technical Reports.
© 2024 PatSnap. All rights reserved.Legal|Privacy policy|Modern Slavery Act Transparency Statement|Sitemap|About US| Contact US: help@patsnap.com