Method for preparing prefabricated rod of gradation type plastic optical fiber
A technology of plastic optical fiber and manufacturing method, which is applied in the field of information and communication, and can solve problems such as limiting the length of preform rods
- Summary
- Abstract
- Description
- Claims
- Application Information
AI Technical Summary
Problems solved by technology
Method used
Examples
Embodiment 1
[0029] (1) 90 volumes of methyl methacrylate, 10 volumes of styrene, 0.05% dibenzoyl peroxide and 0.05% chain transfer agent dodecanethiol were stirred in a vacuum at 45°C for 40 hours in a water bath , and then continued to polymerize at 65° C. under vacuum for 20 hours, pulverized and granulated. And after drying at 95 DEG C for 4 hours, use an extruder to extrude at 220 DEG C, the diameter of the die of the extruder is 2.0 mm, and the rotating speed of the winding wheel is adjusted to obtain a thin rod with a diameter of 2.0 mm. Aging the obtained thin rod at 100°C for 30 minutes to eliminate the internal stress left in the silk, and set it aside.
[0030] (2) Preparation of a series of penetrants:
[0031] ① 91 volumes of methyl methacrylate / 9 volumes of styrene;
[0032] ②92 volumes of methyl methacrylate / 8 volumes of styrene;
[0033] ③94 volumes of methyl methacrylate / 6 volumes of styrene;
[0034] ④ 97 volumes of methyl methacrylate / 3 volumes of styrene;
[0035] ⑤ ...
Embodiment 2
[0040] (1) With 100 parts of styrene (St), the dibenzoyl peroxide of 0.1% by weight, the chain transfer agent dodecanethiol of 0.1% by weight were stirred in 55 ℃ of water baths under vacuum for 20 hours, and then Polymerization was continued at 75° C. for 10 hours under vacuum, crushed and granulated. After drying at 95°C for 4 hours, extrude at 230°C with an extruder. The die diameter of the extruder is 2.0 mm. Adjusting the speed of the winding wheel or the size of the die can make a thin rod with a diameter of 2.0 mm. The obtained thin rods were aged at 100°C for 30 minutes to eliminate the internal stress left in the rods, and they were ready for use.
[0041] (2) Preparation of a series of penetrants:
[0042] ①98 volumes of styrene / 2 volumes of methyl methacrylate;
[0043] ②94 volumes of styrene / 6 volumes of methyl methacrylate;
[0044] ③88 volumes of styrene / 12 volumes of methyl methacrylate;
[0045] ④ 80 volumes of styrene / 20 volumes of methyl methacrylate;
...
Embodiment 3
[0050] (1) With 90 volumes of methyl methacrylate (MMA), 10 volumes of styrene (St), the dibenzoyl peroxide of 0.1% by weight, the chain transfer agent dodecanethiol of 0.1% by weight under vacuum Stir in a water bath at 45°C for 40 hours, then continue to polymerize under vacuum at 65°C for 20 hours, pulverize and granulate. And after drying at 95 DEG C for 4 hours, use an extruder to extrude at 220 DEG C, the diameter of the die of the extruder is 2.0 mm, and the rotating speed of the winding wheel is adjusted to obtain a thin rod with a diameter of 2.0 mm. Aging the obtained thin rod at 100°C for 30 minutes to eliminate the internal stress left in the silk, and set it aside.
[0051] (2) Preparation of a series of penetrants:
[0052] ① 91 volumes of methyl methacrylate / 9 volumes of styrene;
[0053] ②92 volumes of methyl methacrylate / 8 volumes of styrene;
[0054] ③94 volumes of methyl methacrylate / 6 volumes of styrene;
[0055] ④ 97 volumes of methyl methacrylate / 3 vo...
PUM
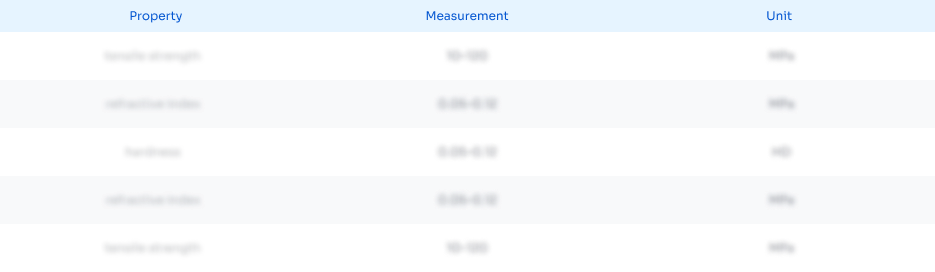
Abstract
Description
Claims
Application Information

- Generate Ideas
- Intellectual Property
- Life Sciences
- Materials
- Tech Scout
- Unparalleled Data Quality
- Higher Quality Content
- 60% Fewer Hallucinations
Browse by: Latest US Patents, China's latest patents, Technical Efficacy Thesaurus, Application Domain, Technology Topic, Popular Technical Reports.
© 2025 PatSnap. All rights reserved.Legal|Privacy policy|Modern Slavery Act Transparency Statement|Sitemap|About US| Contact US: help@patsnap.com