Technology for producing hollow steel by hot squeeze method
A production process and hot extrusion technology, used in metal extrusion forming tools, metal extrusion, manufacturing tools, etc., can solve the problems of poor steel shape and geometric size, low material utilization, and high manufacturing costs, achieving acceptable The effect of improving the force situation, high quality of the inner hole and reducing the production cost
- Summary
- Abstract
- Description
- Claims
- Application Information
AI Technical Summary
Problems solved by technology
Method used
Image
Examples
Embodiment Construction
[0011] As shown in the accompanying drawings, the present invention relates to a new process for producing hollow steel using a hot extrusion machine. Firstly, the electric arc furnace is used to make steel. Lose. Centrifugal casting is then carried out to rotate the molten steel, and a middle hole is naturally formed in the middle of the billet. The casting has a precise structure and no structural defects such as trachoma, pores, and looseness. Then the temperature is adjusted precisely through the industrial frequency furnace to create conditions for the best extrusion force during extrusion, and at the same time avoid the rough structure of the billet. The billet temperature is preferably 1150--1200 °C. Before extrusion molding, first place the billet 4 with the middle hole on the hot extrusion body, wrap the floating mandrel 1 outside the sheath 3 and put it into the extrusion head 2, and the sheath 3 can be made of 3Cr2W8V material . In order to facilitate core pulling...
PUM
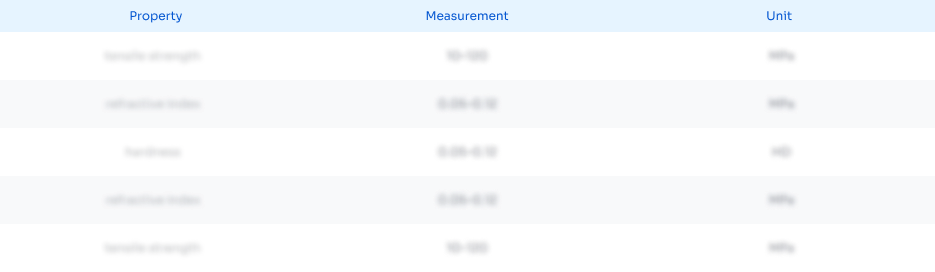
Abstract
Description
Claims
Application Information

- R&D Engineer
- R&D Manager
- IP Professional
- Industry Leading Data Capabilities
- Powerful AI technology
- Patent DNA Extraction
Browse by: Latest US Patents, China's latest patents, Technical Efficacy Thesaurus, Application Domain, Technology Topic, Popular Technical Reports.
© 2024 PatSnap. All rights reserved.Legal|Privacy policy|Modern Slavery Act Transparency Statement|Sitemap|About US| Contact US: help@patsnap.com