Combustion turbine with axial relative movel guide unit
A technology for gas turbines and guiding parts, which is applied in the directions of gas turbine installations, engine components, machines/engines, etc., and can solve problems such as less favorable, large working blade tip clearance, disadvantage, etc.
- Summary
- Abstract
- Description
- Claims
- Application Information
AI Technical Summary
Problems solved by technology
Method used
Image
Examples
Embodiment Construction
[0018] The rotor blade rings 2 are wedged on a turbine shaft 1 (not shown in detail), each rotor blade ring carrying a number of rotor blades 3 . The gas flow 6 guided by the guide vane ring 4 with several guide vanes 5 expands in the gas channel 7 and drives the rotor blades 3 .
[0019] The gas passage 7 has a circular cross-section, and its pressure side end is connected with a hot gas chamber 8. The compressed and heated gas flows out of the hot gas chamber 8 and flows along the direction of the arrow to reach the gas outlet hole 9. The radial inner boundary of the gas channel 7 is formed by the hub 10 of the rotor blade ring 2 wedged on the turbine shaft 1 and the non-rotatable hub 11 of the guide blade ring 4 supported by the inner ends of the guide vanes 5 . The gap between the hubs 10 and 11 is closed with a labyrinth seal.
[0020] The radially outer boundary of the gas channel 7 has a funnel-like cone shape and is formed by rings 12 and 13 . The rings 12 and 13 are...
PUM
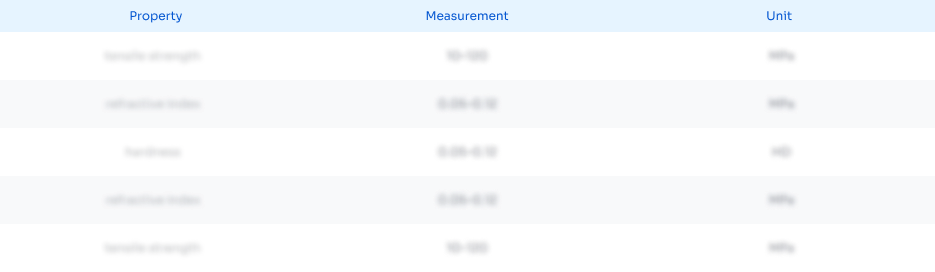
Abstract
Description
Claims
Application Information

- R&D Engineer
- R&D Manager
- IP Professional
- Industry Leading Data Capabilities
- Powerful AI technology
- Patent DNA Extraction
Browse by: Latest US Patents, China's latest patents, Technical Efficacy Thesaurus, Application Domain, Technology Topic, Popular Technical Reports.
© 2024 PatSnap. All rights reserved.Legal|Privacy policy|Modern Slavery Act Transparency Statement|Sitemap|About US| Contact US: help@patsnap.com