Prepn of magnesium hydroxide for fire retardant
A magnesium hydroxide and flame retardant technology, applied in the field of chemical materials, can solve the problems of poor dispersibility and compatibility, large equipment investment and high production cost, and achieve uniform particle size distribution, simple production process and crystallinity. good effect
- Summary
- Abstract
- Description
- Claims
- Application Information
AI Technical Summary
Problems solved by technology
Method used
Image
Examples
Embodiment 1
[0016] The raw material light-burned magnesia and water are fully mixed according to the mass ratio of 1:2. During the stirring process, an aqueous solution of sodium hydroxide equivalent to 2 times the volume of the mixture of light-burned magnesia and water is added dropwise, and the concentration of sodium hydroxide is controlled so that the final The sodium hydroxide concentration of the system is 4M. After stirring for about 30 minutes, it is transferred into a high-pressure reactor with a filling degree of 80%. 160°C, hydrothermal reaction for 10 hours, the resulting product was naturally cooled to room temperature, and then washed and dried to obtain flake magnesium hydroxide for flame retardants. The transmission electron microscope picture of the product is shown in Figure 1a, the scanning electron microscope picture is shown in Figure 2, the electron diffraction pattern is shown in Figure 3, and the XRD spectrum is shown in Figure 4.
Embodiment 2
[0018] The raw material light-burned magnesia and water are fully mixed at a mass ratio of 1:1.5. During the stirring process, an aqueous solution of sodium hydroxide equivalent to 3 times the volume of the mixture of light-burned magnesia and water is added dropwise to control the concentration of sodium hydroxide. Make the sodium hydroxide concentration of the final system 5M, stir for 40 minutes and then transfer to a high-pressure reactor with a filling degree of 75%. Hydrothermal reaction at 170°C for 8 hours, the resulting product was naturally cooled to room temperature, and then washed and dried to obtain flake magnesium hydroxide for flame retardants. The TEM photo of the product is shown in Figure 1b.
Embodiment 3
[0020] The raw material light-burned magnesia and water are fully mixed according to the mass ratio of 1:3. During the stirring process, an aqueous sodium hydroxide solution equivalent to 1.5 times the volume of the mixture of light-burned magnesia and water is added dropwise, and the concentration of sodium hydroxide is controlled so that the final The sodium hydroxide concentration of the system is 6M. After stirring for about 50 minutes, it is transferred into a high-pressure reactor with a filling degree of 80%. 180°C, hydrothermal reaction for 6 hours, the resulting product was naturally cooled to room temperature, and then washed and dried to obtain flake magnesium hydroxide for flame retardants. The TEM photo of the product is shown in Figure 1c.
PUM
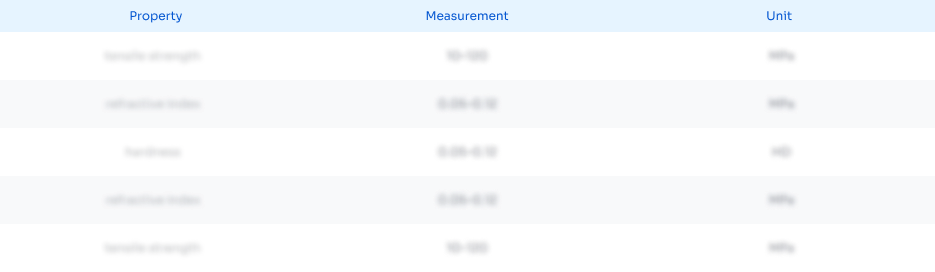
Abstract
Description
Claims
Application Information

- R&D Engineer
- R&D Manager
- IP Professional
- Industry Leading Data Capabilities
- Powerful AI technology
- Patent DNA Extraction
Browse by: Latest US Patents, China's latest patents, Technical Efficacy Thesaurus, Application Domain, Technology Topic, Popular Technical Reports.
© 2024 PatSnap. All rights reserved.Legal|Privacy policy|Modern Slavery Act Transparency Statement|Sitemap|About US| Contact US: help@patsnap.com