Humanoid manipulator mechanism
A robot hand and palm technology, applied in the field of humanoid robot hand mechanism, can solve the problems of unfavorable long-distance transmission, long maintenance cycle, high gear transmission accuracy, and achieve high work flexibility and adaptability, simple structure, and comprehensive functions. Effect
- Summary
- Abstract
- Description
- Claims
- Application Information
AI Technical Summary
Problems solved by technology
Method used
Image
Examples
Embodiment Construction
[0036] The present invention will be further described in detail below in conjunction with the accompanying drawings.
[0037] The invention is a humanoid robot hand mechanism, which has a mechanical structure with five fingers and fourteen joints and three degrees of freedom, and can complete functions similar to human hands. In the present invention, except that the thumb has two knuckles, the remaining four fingers have three knuckles, and the shape of the knuckles is as follows: Figure 7 As shown, the distal knuckle is shaped structure, the middle knuckle is Shaped structure, the proximal knuckle is shaped structure. The connection between knuckles is realized by the shaft hole 801 provided on each knuckle and the respective joint shafts (distal knuckle joint shaft, middle knuckle joint shaft, proximal knuckle joint shaft).
[0038] like figure 1 , 2 As shown, the humanoid robotic hand mechanism is composed of a palm 6, five fingers and a mechanical interface 7. ...
PUM
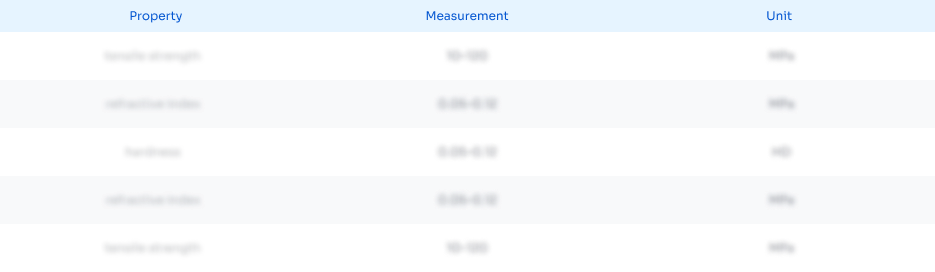
Abstract
Description
Claims
Application Information

- R&D
- Intellectual Property
- Life Sciences
- Materials
- Tech Scout
- Unparalleled Data Quality
- Higher Quality Content
- 60% Fewer Hallucinations
Browse by: Latest US Patents, China's latest patents, Technical Efficacy Thesaurus, Application Domain, Technology Topic, Popular Technical Reports.
© 2025 PatSnap. All rights reserved.Legal|Privacy policy|Modern Slavery Act Transparency Statement|Sitemap|About US| Contact US: help@patsnap.com