Process for preparing isolating wall of plasma display
A plasma and manufacturing method technology, applied in the manufacture of discharge tubes/lamps, cold cathodes, electrode systems, etc., can solve the problem that the uniformity of width and contour is difficult to control, affects the efficiency of discharge cells, and affects the good rate of products, etc. problem, to achieve the effect of more consistent efficiency, improved efficiency, and increased discharge space
- Summary
- Abstract
- Description
- Claims
- Application Information
AI Technical Summary
Problems solved by technology
Method used
Image
Examples
Embodiment Construction
[0024] The following will match Figure 2A to Figure 2G , the method for manufacturing the barrier rib of the present invention will be described in detail.
[0025] First please refer to Figure 2A , forming a plurality of address electrodes 102 on the rear glass substrate 100 . Afterwards, a dielectric layer 104 is covered on the address electrodes 102 to protect the electrodes. Its forming method can be printing method. It should be noted that the dielectric layer 104 has not yet been sintered.
[0026] Then please refer to Figure 2B , at this time, the dielectric layer does not need to be subjected to a high-temperature sintering process, and a layer of photosensitive dry film (photosensitive dry film) 106 is directly formed on the dielectric layer 104. The preferred type is a negative photoresist, and its thickness should be as thick as possible. Thin, about 5 to 30 microns. The photosensitive dry film 106 can be formed by a laminate method.
[0027] Then please r...
PUM
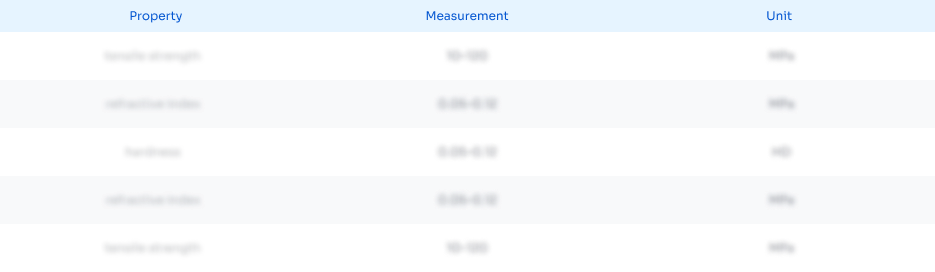
Abstract
Description
Claims
Application Information

- R&D
- Intellectual Property
- Life Sciences
- Materials
- Tech Scout
- Unparalleled Data Quality
- Higher Quality Content
- 60% Fewer Hallucinations
Browse by: Latest US Patents, China's latest patents, Technical Efficacy Thesaurus, Application Domain, Technology Topic, Popular Technical Reports.
© 2025 PatSnap. All rights reserved.Legal|Privacy policy|Modern Slavery Act Transparency Statement|Sitemap|About US| Contact US: help@patsnap.com