Dual-adaptive high-robustness control method for parallel robot
A control method and robot technology, applied in the directions of adaptive control, comprehensive factory control, general control system, etc., can solve problems such as chattering, the dynamic model does not consider the modeling error of parallel robots, mechanism joint friction and external interference, etc. To achieve the effect of reducing overcoming, weakening the chattering of sliding mode control and improving the robustness of the system
- Summary
- Abstract
- Description
- Claims
- Application Information
AI Technical Summary
Problems solved by technology
Method used
Image
Examples
Embodiment 1
[0136] The control method of the present invention mainly focuses on realizing the high robustness motion control of the parallel robot by using a parallel robot dual adaptive high robustness control technology. Taking the parallel robot for automobile electrophoretic coating and conveying as an example, the specific implementation of the control method is as follows:
[0137] 1. Use the analytical method to analyze the kinematic inverse solution of the parallel robot for automobile electrophoretic coating and conveying, and further obtain the positive kinematic solution and Jacobian matrix of the parallel robot
[0138] exist image 3 , the rod length constraint equation is adopted, and the position equation of the mechanism can be obtained according to the structure of the lifting and turning mechanism.
[0139]
[0140] In the formula, L 1 is the length of the connecting rod (unit: m); z i (i=1, 2), β i (i=1, 2) are respectively figure 1 The z-axis position of the t...
PUM
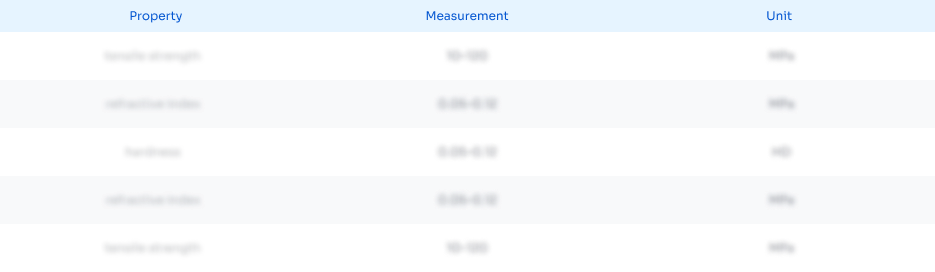
Abstract
Description
Claims
Application Information

- R&D
- Intellectual Property
- Life Sciences
- Materials
- Tech Scout
- Unparalleled Data Quality
- Higher Quality Content
- 60% Fewer Hallucinations
Browse by: Latest US Patents, China's latest patents, Technical Efficacy Thesaurus, Application Domain, Technology Topic, Popular Technical Reports.
© 2025 PatSnap. All rights reserved.Legal|Privacy policy|Modern Slavery Act Transparency Statement|Sitemap|About US| Contact US: help@patsnap.com