Insulating coating coating device for wire processing
A technology of insulating coating and coating device, which is applied in the direction of insulating conductors/cables, circuits, electrical components, etc., can solve the problems of reduced drying structure performance, reduced drying efficiency, difficult maintenance of control components, etc.
- Summary
- Abstract
- Description
- Claims
- Application Information
AI Technical Summary
Problems solved by technology
Method used
Image
Examples
Embodiment 1
[0046] The present invention provides an insulating coating coating device for wire processing, comprising: a base 1, a driving part 3 and a drying part 5;
[0047] The base 1 is fixedly connected to the workbench through four fixing bolts 101, and two supporting wheels A103 are installed on the top surface of the base 1;
[0048] A mounting bracket A104 is installed on the top surface of the base 1, and the mounting bracket A104 is aligned with the supporting wheel A103 on the left side, and a supporting wheel B105 is installed on the mounting bracket A104;
[0049] Wire 2 is transported between the roller B105 and the roller A103;
[0050]The driving part 3 is composed of a mounting frame B301, a driving wheel 302, a driving motor 303 and a groove 304, and the mounting frame B301 is installed on the top surface of the base 1;
[0051] A bracket 4 is installed on the top surface of the base 1;
[0052] The drying part 5 consists of a frame body 501, a connecting rod 502, a ...
Embodiment 2
[0065] An insulating coating coating device for wire processing, further comprising: a supplying part 6; 601 is mounted on mounting bracket A104.
[0066] Furthermore, according to embodiments of the present invention, such as figure 2 As shown, the liquid storage box 604 is fixedly connected to the rear end face of the mounting bracket A104;
[0067] The piston bottle 601 is connected with a nozzle 602 and a water inlet pipe, and the water inlet pipe is connected with the liquid storage box 604, and the head end of the nozzle 602 is inserted into the coated cotton 401;
[0068] A check valve is installed in the spray pipe 602 and the water inlet pipe, so that the automatic liquid supply of the coated cotton 401 can be realized when the piston bottle 601 is stretched and retracted.
[0069] Furthermore, according to embodiments of the present invention, such as figure 2 As shown, the piston bottle 601 is welded with a connecting arm 603, and the tail end of the connecting...
Embodiment 3
[0075] An insulating coating coating device for wire processing, further comprising: an auxiliary part 7 ;
[0076] Furthermore, according to embodiments of the present invention, such as Image 6 As shown, the telescopic bottle 701 is fixedly connected to the bottom end surface of the mounting frame B301, and the telescopic bottle 701 is connected with a connecting pipe 702; the connecting pipe 702 is connected with a spray head 703, and the spray head 703 is a ring structure; the inside of the spray head 703 is opened in a circular array shape There are air jet holes, and the nozzle 703 is sleeved on the outside of the wire 2;
[0077] A force block 704 is installed at the head end of the telescopic bottle 701, and the force block 704 is elastically clamped with the groove 304, and when the driving wheel 302 rotates, the telescoping bottle 701 continuously expands and contracts under the action of the force block 704 and the groove 304 Then, at this time, the gas in the tel...
PUM
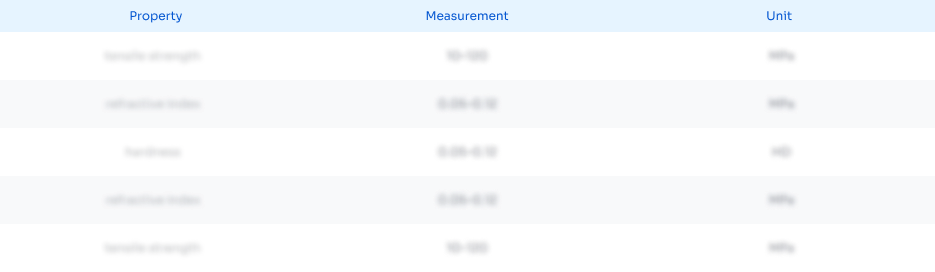
Abstract
Description
Claims
Application Information

- R&D
- Intellectual Property
- Life Sciences
- Materials
- Tech Scout
- Unparalleled Data Quality
- Higher Quality Content
- 60% Fewer Hallucinations
Browse by: Latest US Patents, China's latest patents, Technical Efficacy Thesaurus, Application Domain, Technology Topic, Popular Technical Reports.
© 2025 PatSnap. All rights reserved.Legal|Privacy policy|Modern Slavery Act Transparency Statement|Sitemap|About US| Contact US: help@patsnap.com