Spiral groove gas dynamic pressure bearing test device
A gas dynamic pressure bearing and test device technology, which is applied in mechanical bearing testing, measuring devices, testing of mechanical components, etc., can solve problems such as precise control of rotor speed, unstable speed, and influence on test accuracy
- Summary
- Abstract
- Description
- Claims
- Application Information
AI Technical Summary
Problems solved by technology
Method used
Image
Examples
Embodiment 1
[0047] Reference Figure 1-Figure 4 The example of this embodiment is used to provide a spiral groove bearing test device.
[0048] like figure 1 The section of the spiral groove bearing for the test to be tested is a spherical spiral groove gas dynamic storm bearing, including the stator 23 and the rotor 34. Both have standard spherical sphere. 23 gaps in the stator. A fixed setting of the Rotary 34 Star 23 is set with a driving shaft 341, a fixed setting of the side of the stator 23 with a load shaft 342, and the load shaft 342 runs through the stator 23. Rotor 34, driving shaft 341 and load shaft 342 common axis. Because the spiral grooves of the spiral groove bearing are shallow, therefore figure 1 No display.
[0049] like figure 2 As well as image 3 The test device includes support base 1, support base 1 to support the invention on the ground or countertop. Support base 1 includes the bottom board 11 and the standing board 12, the bottom board 11 level settings, the standing ...
Embodiment 2
[0069] Reference Figure 5-Figure 7 Compared with the Example 1, the spiral groove bearing test device provided by this embodiment has been improved compared to the embodiment 1: it can also test the spherical spiral gases of the spherical pipe gases with a angle spiral groove of the stator 23 and the rotor 34.
[0070] Compared with the cone spiral groove bearing, the spherical spiral groove bearing is still working properly even between the stator 23 and the rotor 34. The performance in this case also needs to pass test verification. like Figure 5 The sphere of spherical spiral groove bearing of the spherical spiral groove of the embodiment of this embodiment, the stator 23 and the rotor 34 set the settings, both have standard sphere, but the two are in a non -coaxial state with angle, and the rotor 34 34 There is no load shaft 342 on the top.
[0071] like Image 6 The assembly diagram (explosion map) of the rotary bracket 2 and its internal and external components, the bearing b...
PUM
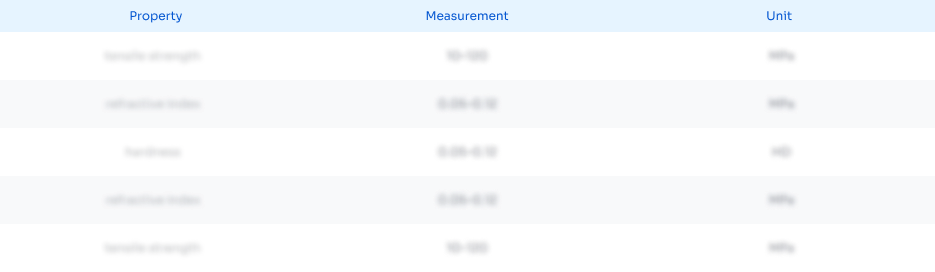
Abstract
Description
Claims
Application Information

- R&D
- Intellectual Property
- Life Sciences
- Materials
- Tech Scout
- Unparalleled Data Quality
- Higher Quality Content
- 60% Fewer Hallucinations
Browse by: Latest US Patents, China's latest patents, Technical Efficacy Thesaurus, Application Domain, Technology Topic, Popular Technical Reports.
© 2025 PatSnap. All rights reserved.Legal|Privacy policy|Modern Slavery Act Transparency Statement|Sitemap|About US| Contact US: help@patsnap.com