Robot flexible joint friction force analysis and modeling method
A technology of flexible joints and modeling methods, applied in the field of robotics, can solve the problems of low accuracy of dynamic models, achieve the effect of improving control accuracy and stability, and improving accuracy
- Summary
- Abstract
- Description
- Claims
- Application Information
AI Technical Summary
Problems solved by technology
Method used
Image
Examples
Embodiment 1
[0087] see figure 1 , which is a flowchart of the method for analyzing and modeling the friction force of a flexible joint of a robot in this embodiment. The method for analyzing and modeling the friction force of the robot flexible joint includes the following steps, namely S1-S7.
[0088] S1: Collect the state data of the robot's flexible joints. Status data includes: overall status data, motor status data, load status data and flexible transmission element status data. The overall state data includes generalized coordinates, generalized velocity, generalized acceleration, joint rotation angle, joint angular velocity, joint angular acceleration, joint motion velocity, flexible joint radius, static friction coefficient, Coulomb friction coefficient and viscous friction coefficient; motor state data includes the input of the motor Torque, rotation angle of the motor end, angular velocity of the motor end, angular acceleration of the motor end, moment of inertia of the motor ...
PUM
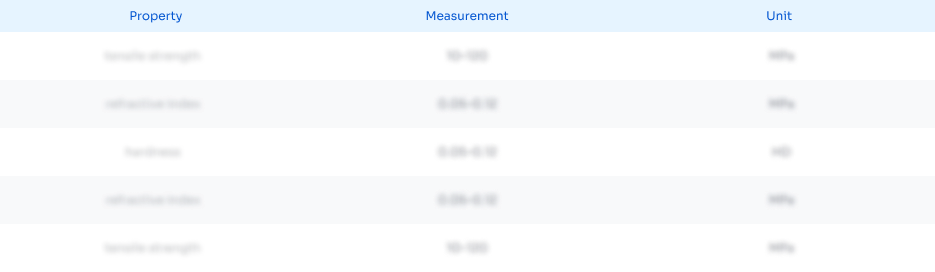
Abstract
Description
Claims
Application Information

- R&D Engineer
- R&D Manager
- IP Professional
- Industry Leading Data Capabilities
- Powerful AI technology
- Patent DNA Extraction
Browse by: Latest US Patents, China's latest patents, Technical Efficacy Thesaurus, Application Domain, Technology Topic, Popular Technical Reports.
© 2024 PatSnap. All rights reserved.Legal|Privacy policy|Modern Slavery Act Transparency Statement|Sitemap|About US| Contact US: help@patsnap.com