Cast-in-place combined pavement slab for airport and preparation method
A cast-in-place, airport technology, applied in the direction of roads, roads, special pavements, etc., can solve the problems of foundation soil settlement, time-consuming and laborious, plate fracture, etc., and achieve the effect of reducing tensile cracking, comfortable passenger environment, and reducing FOD.
- Summary
- Abstract
- Description
- Claims
- Application Information
AI Technical Summary
Problems solved by technology
Method used
Image
Examples
Embodiment 1
[0021] like figure 1 As shown, the airport cast-in-place composite road panel provided in this embodiment is composed of an upper layer 1 and a lower layer 3 made of engineering cement-based composite materials and an intermediate layer 2 made of dry hard concrete; the upper layer 1 and the lower layer 3 are both It is composed of water, cement, fly ash, quartz sand, HCSA expansion agent, PVA fiber and polycarboxylate water reducer, among which water, cement, fly ash, quartz sand, HCSA expansion agent and polycarboxylate water reducer are The weight ratio is 35:40:50:35:12:0.2, and the volume content of PVA fiber accounts for 2% of the total volume of the upper or lower layer. Among them, Portland cement of 42.5 strength grade is used for cement; first-grade fly ash is used for fly ash; and 90-mesh fine quartz sand is used for quartz sand. The thickness of the upper layer 1, the middle layer 2 and the lower layer 3 is determined according to the airport class and the required...
Embodiment 2
[0029] like figure 1 As shown, the airport cast-in-place composite road panel provided in this embodiment is composed of an upper layer 1 and a lower layer 3 made of engineering cement-based composite materials and an intermediate layer 2 made of dry hard concrete; the upper layer 1 and the lower layer 3 are both It is composed of water, cement, fly ash, quartz sand, HCSA expansion agent, PVA fiber and polycarboxylate water reducer, among which water, cement, fly ash, quartz sand, HCSA expansion agent and polycarboxylate water reducer are The weight ratio is 40:45:55:40:15:0.2, and the volume content of PVA fiber accounts for 1.5% of the total volume of the upper or lower layer. Among them, Portland cement of 42.5 strength grade is used for cement; first-grade fly ash is used for fly ash; and 100-mesh fine quartz sand is used for quartz sand. The thickness of the upper layer 1, the middle layer 2 and the lower layer 3 is determined according to the airport class and the requi...
Embodiment 3
[0032] like figure 1 As shown, the airport cast-in-place composite road panel provided in this embodiment is composed of an upper layer 1 and a lower layer 3 made of engineering cement-based composite materials and an intermediate layer 2 made of dry hard concrete; the upper layer 1 and the lower layer 3 are both It is composed of water, cement, fly ash, quartz sand, HCSA expansion agent, PVA fiber and polycarboxylate water reducer, among which water, cement, fly ash, quartz sand, HCSA expansion agent and polycarboxylate water reducer are The weight ratio is 30:35:45:30:10:0.1, and the volume dosage of PVA fiber accounts for 1% of the total volume of the upper or lower layer. Among them, Portland cement of 42.5 strength grade is used for cement; first-grade fly ash is used for fly ash; and 120-mesh fine quartz sand is used for quartz sand. The thickness of the upper layer 1, the middle layer 2 and the lower layer 3 is determined according to the airport class and the required...
PUM
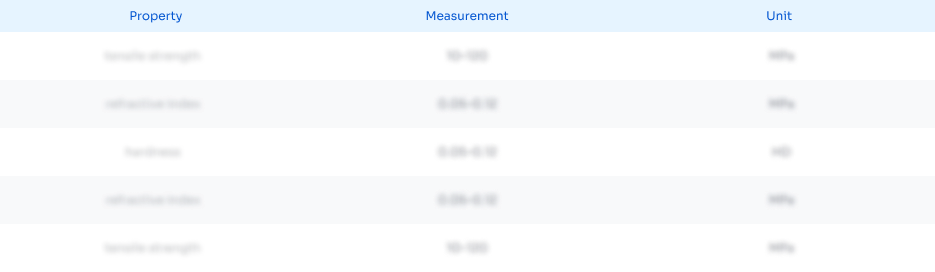
Abstract
Description
Claims
Application Information

- R&D Engineer
- R&D Manager
- IP Professional
- Industry Leading Data Capabilities
- Powerful AI technology
- Patent DNA Extraction
Browse by: Latest US Patents, China's latest patents, Technical Efficacy Thesaurus, Application Domain, Technology Topic, Popular Technical Reports.
© 2024 PatSnap. All rights reserved.Legal|Privacy policy|Modern Slavery Act Transparency Statement|Sitemap|About US| Contact US: help@patsnap.com