Clamp module for numerical control lathe and workpiece clamping method
A fixture module and CNC lathe technology, applied in the field of machine tools, can solve problems such as clamping deflection of shaft parts, affecting product processing accuracy and errors, and achieve the effects of ensuring accuracy, reducing load, and good operation convenience
- Summary
- Abstract
- Description
- Claims
- Application Information
AI Technical Summary
Problems solved by technology
Method used
Image
Examples
Embodiment Construction
[0040] The technical solutions in the embodiments of the present invention will be clearly and completely described below with reference to the accompanying drawings in the embodiments of the present invention. Obviously, the described embodiments are only a part of the embodiments of the present invention, rather than all the embodiments. Based on the embodiments of the present invention, all other embodiments obtained by those of ordinary skill in the art without creative efforts shall fall within the protection scope of the present invention.
[0041] figure 1 A schematic diagram of the three-dimensional structure of a fixture module for a numerically controlled lathe according to an embodiment of the present invention is shown.
[0042] Specifically, the present invention provides a fixture module for a numerically controlled lathe, which is installed on the main body of the numerically controlled machine tool. Specifically, the main body of the numerically controlled mach...
PUM
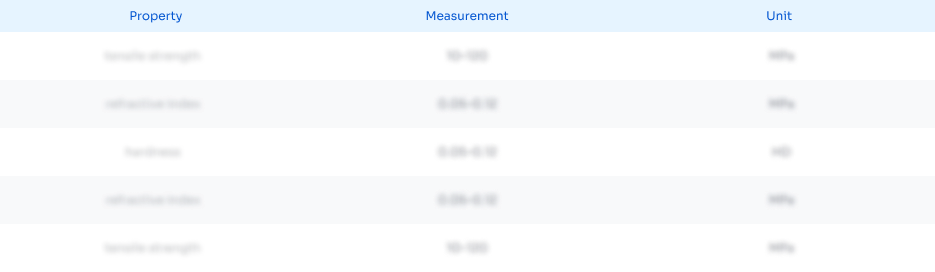
Abstract
Description
Claims
Application Information

- R&D
- Intellectual Property
- Life Sciences
- Materials
- Tech Scout
- Unparalleled Data Quality
- Higher Quality Content
- 60% Fewer Hallucinations
Browse by: Latest US Patents, China's latest patents, Technical Efficacy Thesaurus, Application Domain, Technology Topic, Popular Technical Reports.
© 2025 PatSnap. All rights reserved.Legal|Privacy policy|Modern Slavery Act Transparency Statement|Sitemap|About US| Contact US: help@patsnap.com