Multi-arm collaborative flexible cable obstacle crossing operation robot
An operation robot and flexible cable technology, applied in the field of robotics, can solve the problems of the ground personnel being far away from the flexible cable, inconvenient inspection of the flexible cable, and cumbersome operating procedures, etc., achieving short obstacle surmounting time, high inspection accuracy, and improved safety and stability sexual effect
- Summary
- Abstract
- Description
- Claims
- Application Information
AI Technical Summary
Problems solved by technology
Method used
Image
Examples
Embodiment Construction
[0045] The present invention proposes a multi-arm cooperative flexible cable obstacle crossing robot. In order to make the advantages and technical solutions of the present invention clearer and clearer, the present invention will be described in detail below with reference to specific embodiments.
[0046] like Figure 1-2 As shown in the figure, a multi-arm cooperative flexible cable obstacle crossing operation robot includes a frame-type box 5, and the top of the frame-type box 5 is provided with a sliding swing mechanism 4, and the sliding swing mechanism 4 is connected with a front moving arm 1, a middle moving arm Arm 2 and the back movement arm;
[0047] The front moving arm 1 and the rear moving arm are symmetrically arranged on the front and rear sides of the frame-type box 5, and the front moving arm 1 and the rear moving arm have completely the same structure. The cable mechanism 12, the first swing mechanism 139 and the first lifting mechanism 13; the moving arm f...
PUM
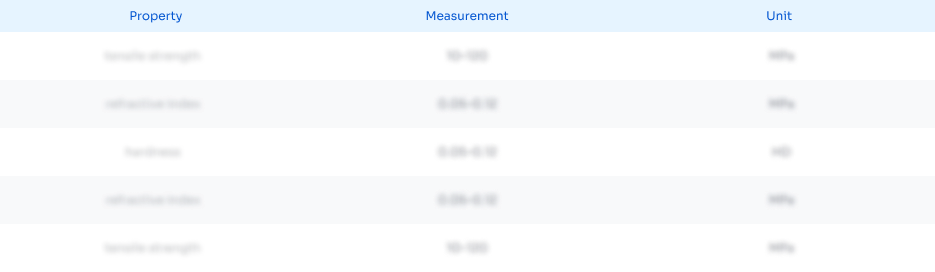
Abstract
Description
Claims
Application Information

- R&D Engineer
- R&D Manager
- IP Professional
- Industry Leading Data Capabilities
- Powerful AI technology
- Patent DNA Extraction
Browse by: Latest US Patents, China's latest patents, Technical Efficacy Thesaurus, Application Domain, Technology Topic, Popular Technical Reports.
© 2024 PatSnap. All rights reserved.Legal|Privacy policy|Modern Slavery Act Transparency Statement|Sitemap|About US| Contact US: help@patsnap.com