Large-view-field stereoscopic vision calibration method
A technology of stereo vision and calibration method, applied in the field of three-dimensional measurement, can solve the problems of heavy weight, cumbersome operation, large temperature space gradient, etc., and achieve the effect of high-efficiency calibration and optimization of external parameters
- Summary
- Abstract
- Description
- Claims
- Application Information
AI Technical Summary
Problems solved by technology
Method used
Image
Examples
Embodiment 1
[0055] A large field of view stereo vision calibration method, comprising the following steps:
[0056]S1. Establish the relationship between the camera model coordinate system and the pixel coordinate system;
[0057] S2. Perform image distortion correction;
[0058] S3. Paste the coding point and the marking point evenly in the field of view to be measured, to ensure that the coding point and the marking point cover the range to be measured as much as possible, and then use the monocular photogrammetry system to measure to obtain the three-dimensional space coordinates of the coding point and the marking point;
[0059] S4. Use the stereo vision measurement system to measure, and establish the corresponding relationship between the marker points in different camera images after completing the decoding of the encoded marker points, and calculate the rough pose relationship of the image detection;
[0060] S5. Solve the matrix of the pose relationship;
[0061] S6. Use the 8...
Embodiment 2
[0069] S1 as figure 1 As shown, in the stereo vision measurement system, the camera imaging process is generally represented by a pinhole imaging model. 3D point M=[x,y,z] T and its pixel coordinates m=[u,v] T The relationship between can be expressed as
[0070]
[0071] Among them, s is the scale factor, m is the measured pixel coordinate value, and m' is the theoretical pixel coordinate value. In the actual measurement process, m can be corrected to the theoretical value m' by nonlinear lens distortion. The k vector is the lens distortion parameter, [R|t] is the camera extrinsic parameter matrix, and A is the camera intrinsic parameter matrix.
[0072]
[0073] Among them, (u 0 ,v 0 ) the pixel coordinates of the main point, α x with alpha y are the normalized focal lengths in the horizontal and vertical directions of the camera, respectively, and γ represents the angle between the two axes of the camera image.
[0074] S2 uses the following formula for image...
PUM
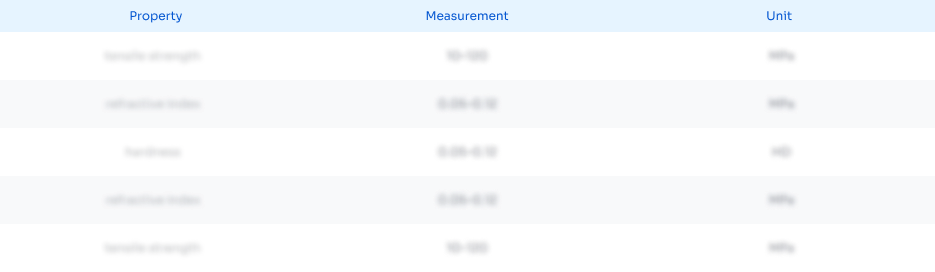
Abstract
Description
Claims
Application Information

- Generate Ideas
- Intellectual Property
- Life Sciences
- Materials
- Tech Scout
- Unparalleled Data Quality
- Higher Quality Content
- 60% Fewer Hallucinations
Browse by: Latest US Patents, China's latest patents, Technical Efficacy Thesaurus, Application Domain, Technology Topic, Popular Technical Reports.
© 2025 PatSnap. All rights reserved.Legal|Privacy policy|Modern Slavery Act Transparency Statement|Sitemap|About US| Contact US: help@patsnap.com