Method and system for co-processing hazardous waste through rotary kiln and sintering machine
A co-processing and hazardous waste technology, which is applied in the direction of combustion method, combustion type, lighting and heating equipment, etc., can solve the problems of abnormal production, low heat utilization rate of organic matter, secondary pollution, etc., and improve the effect of pyrolysis and incineration , enhance the gas mixing effect, accelerate the effect of combustion reaction
- Summary
- Abstract
- Description
- Claims
- Application Information
AI Technical Summary
Problems solved by technology
Method used
Image
Examples
Embodiment 1
[0133] like Figure 2-3 , 5, a rotary kiln-sintering machine co-processing hazardous waste system, the system includes rotary kiln C1. The rotary kiln C1 includes a kiln head 1 , a kiln body 2 and a kiln tail 3 . The kiln head 1 is provided with a material inlet 101 . The kiln body 2 includes a furnace lining 201 and a furnace hearth 202 . The kiln tail 3 is provided with a material outlet 301 and a material discharge air duct 302 . The material outlet 301 is located at the bottom of the kiln tail 3 . The discharge air duct 302 is located at the upper part of the material outlet 301 , and the discharge air duct 302 communicates with the material outlet 301 . Along the material direction, the furnace chamber 202 is divided into a pyrolysis chamber 20201 and an incineration chamber 20202 . The inside of the furnace lining 201 corresponding to the pyrolysis chamber 20201 is provided with an air duct 4 in the kiln. One end of the air duct 4 in the kiln extends into the kiln ...
Embodiment 2
[0136] Example 1 is repeated, except that four secondary air ducts 7 are separated from the primary air duct 6 . The four secondary air ducts 7 are annularly distributed around the material inlet 101 .
Embodiment 3
[0138] Example 2 is repeated, except that the rotary kiln C1 is provided with 10 air ducts 4 in the kiln. The 10 air ducts 4 in the kiln are evenly distributed along the circumferential direction of the rotary kiln C1. Each air duct 4 in the kiln communicates with the annular air duct 5 arranged on the kiln head 1 .
PUM
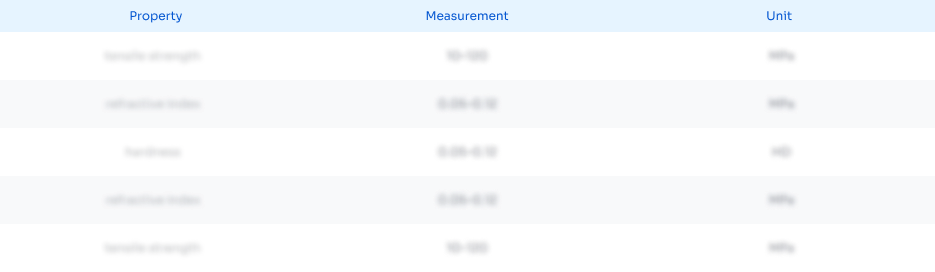
Abstract
Description
Claims
Application Information

- R&D
- Intellectual Property
- Life Sciences
- Materials
- Tech Scout
- Unparalleled Data Quality
- Higher Quality Content
- 60% Fewer Hallucinations
Browse by: Latest US Patents, China's latest patents, Technical Efficacy Thesaurus, Application Domain, Technology Topic, Popular Technical Reports.
© 2025 PatSnap. All rights reserved.Legal|Privacy policy|Modern Slavery Act Transparency Statement|Sitemap|About US| Contact US: help@patsnap.com