Core body structure of automobile auxiliary frame mold
A sub-frame and core technology is applied in the field of core structure of automobile sub-frame molds, which can solve the problems of inconsistent thickness of sub-frames and achieve the effect of uniform material distribution.
- Summary
- Abstract
- Description
- Claims
- Application Information
AI Technical Summary
Problems solved by technology
Method used
Image
Examples
Embodiment Construction
[0024] Attached to the following Figure 1-4 This application will be described in further detail.
[0025] The present application discloses a core structure of an automobile subframe mold, refer to figure 1 , figure 2 , the structure includes a core body, the core body is composed of an upper core body 1 and a lower core body 2, the upper core body and the lower core body are buckled with each other, the four corners of the core body are provided with positioning components, the upper core body 1 and the lower core body are There are pressure detection components between the core bodies 2, the number of pressure detection components between the upper core body 1 and the lower core body 2 is multiple, and the multiple pressure detection components are evenly distributed between the upper core body 1 and the lower core body 2 Arrangement, the pressure detection assembly includes a support column 3 installed on the inner side of the upper core body 1, a support sleeve 4 inst...
PUM
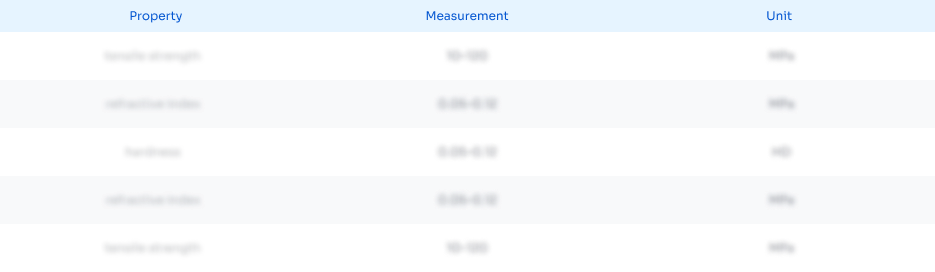
Abstract
Description
Claims
Application Information

- R&D
- Intellectual Property
- Life Sciences
- Materials
- Tech Scout
- Unparalleled Data Quality
- Higher Quality Content
- 60% Fewer Hallucinations
Browse by: Latest US Patents, China's latest patents, Technical Efficacy Thesaurus, Application Domain, Technology Topic, Popular Technical Reports.
© 2025 PatSnap. All rights reserved.Legal|Privacy policy|Modern Slavery Act Transparency Statement|Sitemap|About US| Contact US: help@patsnap.com