800 kW axial flow air turbine based on multi-stage small enthalpy drop blade structure
A blade structure and air turbine technology, which is applied to blade support elements, machines/engines, and leakage prevention. It can solve the difficult problems of high-efficiency axial flow turbines, and achieve the improvement of single-stage blade efficiency and air level. Effect of reduction in working ability and secondary flow loss
- Summary
- Abstract
- Description
- Claims
- Application Information
AI Technical Summary
Problems solved by technology
Method used
Image
Examples
specific Embodiment approach 1
[0028] Embodiment 1: Combining Figure 1-Figure 4 Illustrating this embodiment, the 800kW axial flow air turbine based on the multi-stage small enthalpy drop vane structure includes a front bearing box 1, a front end shaft seal 2, a cylinder 3, a stationary blade assembly 4, a moving blade assembly 5, Rotor 6, rear end shaft seal 7, rear bearing box 8 and platform base 9;
[0029] The front bearing box 1 is mounted on the front end of the cylinder 3, the rear bearing box 8 is mounted on the rear end of the cylinder 3, the stationary vane assembly 4 is mounted on the inner wall of the cylinder 3, the moving vane assembly 5 is sleeved on the outer wall of the rotor 6, and the rotor 6 is horizontally installed in the cylinder 3, the front end of the rotor 6 is rotatably connected and inserted in the front bearing box 1, the rear end of the rotor 6 is rotatably inserted in the rear bearing box 8, and the moving blade assembly 5 on the outer side wall of the rotor 6 is connected wi...
specific Embodiment approach 2
[0031] Specific implementation mode 2: Combining Figure 4 Illustrating this embodiment, an 800kW axial flow air turbine based on a multi-stage small enthalpy drop blade structure described in this embodiment further includes a front thrust support combined bearing 1-1 and a rear support bearing 8-1; the front thrust support The joint bearing 1-1 is installed in the front bearing box 1, and the rear support bearing 8-1 is installed in the rear bearing box 8. The front end of the rotor 6 is rotatably connected with the front bearing box 1 through the front thrust support joint bearing 1-1. The end is rotatably connected to the rear bearing housing 8 through the rear support bearing 8-1. Other compositions and connection methods are the same as those in the first embodiment.
specific Embodiment approach 3
[0032] Specific implementation three: combination Figure 4 Illustrating this embodiment, an 800kW axial flow air turbine based on a multi-stage small enthalpy drop vane structure described in this embodiment, the front end and rear end of the cylinder 3 are respectively supported on the front bearing box 1 and the rear bearing box 8 through cat claws superior. The lower half of the cylinder 3 is connected with the front and rear bearing housings through guide keys. The cylinder 3 in this embodiment adopts a single-layer cylinder structure, which can adapt to the characteristics of the working environment of 535°C / 0.75MPa at the inlet of the turbine and 0.2MPa at the outlet. Other compositions and connection modes are the same as those in the second embodiment.
PUM
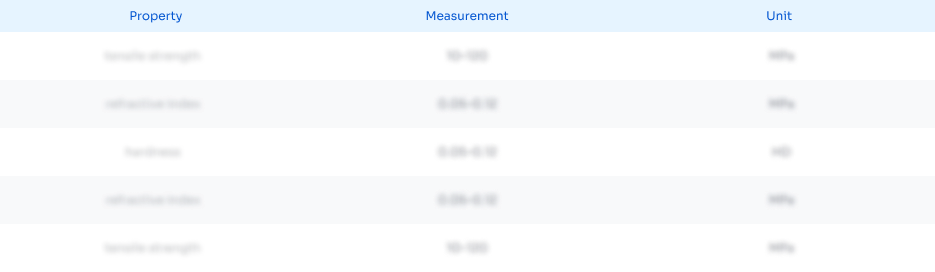
Abstract
Description
Claims
Application Information

- R&D Engineer
- R&D Manager
- IP Professional
- Industry Leading Data Capabilities
- Powerful AI technology
- Patent DNA Extraction
Browse by: Latest US Patents, China's latest patents, Technical Efficacy Thesaurus, Application Domain, Technology Topic, Popular Technical Reports.
© 2024 PatSnap. All rights reserved.Legal|Privacy policy|Modern Slavery Act Transparency Statement|Sitemap|About US| Contact US: help@patsnap.com