Preparation method of catalyst for preparing acrylic acid through selective oxidation of propane
A selectivity and catalyst technology, applied in the direction of catalyst activation/preparation, preparation of organic compounds, physical/chemical process catalysts, etc., can solve the problems of poor selectivity and low catalyst activity
- Summary
- Abstract
- Description
- Claims
- Application Information
AI Technical Summary
Problems solved by technology
Method used
Image
Examples
Embodiment 1
[0050] The first step: dissolve-co-precipitation method prepares catalyst slurry I of the present invention
[0051] Add 141.5 g of ammonium molybdate, 23.1 g of ammonium metavanadate, 43.4 g of telluric acid and 40 ml of water to the No. 1 beaker, stir the mixture at 75 to 80°C to dissolve it, and add 125.6 g of niobium oxalate and Stir 50ml of distilled water at 75-80℃ to dissolve, then slowly add the solution in the No. 2 beaker dropwise to the No. 1 beaker, continue to add distilled water to 100ml, and react at normal pressure for 2 hours to obtain a compound containing multiple components Metal oxide catalyst slurry I;
[0052] Step 2: Preparation containing NiSb 2 O 6 Structural Slurry II
[0053] 9 g of oxalic acid (H 2 C 2 O 4 ), 146.1g nickel nitrate (Ni(NO 3 ) 2 ), 58.32g antimony oxide (Sb 2 O 3 ) and 900ml of deionized water in a 1000ml beaker to mix evenly, then adjust the pH of the solution to 2, and react at 55 to 60°C under normal pressure for 2.5h to...
Embodiment 2
[0068] The first step: dissolve-co-precipitation method prepares catalyst slurry I of the present invention
[0069] Add 150 g of ammonium molybdate, 23.1 g of ammonium metavanadate, 45.9 g of telluric acid and 45 ml of water to the No. 1 beaker, stir the mixture at 75 to 80°C to dissolve it, and add 138.1 g and 50 ml of niobium oxalate to the No. 2 beaker Stir the distilled water at 80-85°C to dissolve it, then slowly add the solution in the No. 2 beaker dropwise to the No. 1 beaker, continue to add distilled water to 100ml, and react at normal pressure for 2.5h to obtain a multi-component compound Metal oxide catalyst slurry I;
[0070] Step 2: Preparation containing NiSb 2 O 6 Structural Slurry II
[0071] 9 g of oxalic acid (H 2 C 2 O 4 ), 182.7g nickel nitrate (Ni(NO 3 ) 2 ), 58.32g antimony oxide (Sb 2 O 3 ) and 900ml of deionized water in a 1000ml beaker to mix evenly, then adjust the pH of the solution to 1.5, and react at 55 to 60°C under normal pressure for...
Embodiment 3
[0090] The first step: dissolve-co-precipitation method prepares catalyst slurry I of the present invention
[0091] 158.9 g of ammonium molybdate, 25.7 g of ammonium metavanadate, 45.9 g of telluric acid and 50 ml of water were added to the No. 1 beaker, and the mixture was stirred at 85 to 90°C to dissolve it. In the No. 2 beaker, 150.7 g of niobium oxalate and Stir 50ml of distilled water at 80-85°C to dissolve, then slowly add the solution in the No. 2 beaker dropwise to the No. 1 beaker, continue to add distilled water to 100ml, and react at normal pressure for 1.5h to obtain a multi-component solution. Composite metal oxide catalyst slurry I;
[0092] Step 2: Preparation containing NiSb 2 O 6 Structural Slurry II
[0093] 9 g of oxalic acid (H 2 C 2 O 4 ), 219.2g nickel nitrate (Ni(NO 3 ) 2 ), 58.32g antimony oxide (Sb 2 O 3 ) and 900ml of deionized water in a 1000ml beaker to mix evenly, then adjust the pH of the solution to 1, after mixing, react at 60-65°C a...
PUM
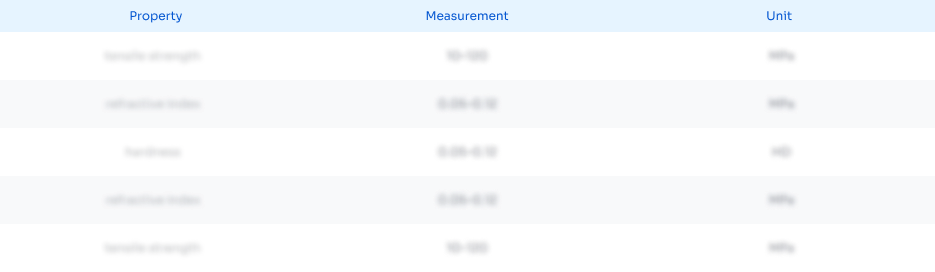
Abstract
Description
Claims
Application Information

- R&D
- Intellectual Property
- Life Sciences
- Materials
- Tech Scout
- Unparalleled Data Quality
- Higher Quality Content
- 60% Fewer Hallucinations
Browse by: Latest US Patents, China's latest patents, Technical Efficacy Thesaurus, Application Domain, Technology Topic, Popular Technical Reports.
© 2025 PatSnap. All rights reserved.Legal|Privacy policy|Modern Slavery Act Transparency Statement|Sitemap|About US| Contact US: help@patsnap.com