Weld defect automatic detection method and device
An automatic detection and visual detection device technology, applied in the direction of measuring devices, optical testing defects/defects, instruments, etc., can solve problems such as inability to trace back, analyze welds, improve welding processes, and not conform to equipment intelligence, etc., to achieve improved welding The effect of weld quality, ease of evaluation and monitoring
- Summary
- Abstract
- Description
- Claims
- Application Information
AI Technical Summary
Problems solved by technology
Method used
Image
Examples
Embodiment 1
[0035] Embodiment 1: Reference figure 1 , an automatic detection method for weld defects, comprising the following steps:
[0036] S1: Obtain the preset welding trajectory and process parameters during the welding operation of the welding robot and store them in a separate server, obtain the actual welding trajectory during the welding operation of the welding robot and store them in a separate server;
[0037] S2: Use the welding seam visual inspection device and ultrasonic flaw detector to scan and detect the weld seam following the preset welding trajectory of the welding robot obtained in step S1, and upload the weld seam inspection data to the server for storage. The device detects the appearance parameters of the weld, and the ultrasonic flaw detector detects the internal parameters of the weld;
[0038] S3: Tabulate the preset welding trajectory, actual welding trajectory, process parameters and weld inspection data saved in the server during the welding operation of t...
Embodiment 2
[0043] Embodiment 2: Reference Figure 4, an automatic detection device for weld defects, comprising a welding robot 1, a weld visual inspection device 2, an ultrasonic flaw detector 3, a detection platform 4, an edge module 7, a server 5 and a computer 8, the detection platform 4 is used to fix a workpiece 6, There are three welding robots 1, one of which is used for welding, and the other two are used to install the weld visual inspection device 2 and the ultrasonic flaw detector 3 respectively. The detection data of the weld seam visual inspection device 2 and the ultrasonic flaw detector 3 are transmitted to the welding robot. The robot 1 is uploaded to the server 5 by the edge module 7, and the server 5 is used for the actual welding trajectory, process parameters, weld appearance parameters detected by the welding seam visual inspection device 2 and ultrasonic flaw detection of the welding robot 1 during the welding operation. The internal parameters of the weld detected...
PUM
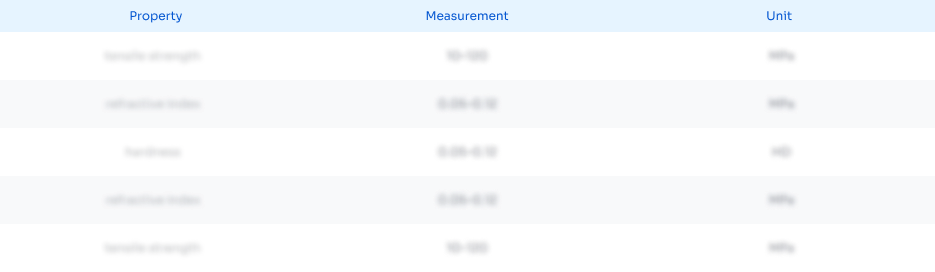
Abstract
Description
Claims
Application Information

- R&D
- Intellectual Property
- Life Sciences
- Materials
- Tech Scout
- Unparalleled Data Quality
- Higher Quality Content
- 60% Fewer Hallucinations
Browse by: Latest US Patents, China's latest patents, Technical Efficacy Thesaurus, Application Domain, Technology Topic, Popular Technical Reports.
© 2025 PatSnap. All rights reserved.Legal|Privacy policy|Modern Slavery Act Transparency Statement|Sitemap|About US| Contact US: help@patsnap.com