Micromechanical z-axis inertial sensor and method for producing such sensor
A technology of micro-mechanics and axis inertia, which is applied in the direction of acceleration measurement, instrumentation, and micro-structure technology using inertial force, and can solve problems such as inability to accurately limit stop behavior and cost
- Summary
- Abstract
- Description
- Claims
- Application Information
AI Technical Summary
Problems solved by technology
Method used
Image
Examples
Embodiment Construction
[0032] In the following, in order to describe the geometric relationship, it is considered that the substrate plane of the proposed micromechanical z-axis inertial sensor extends in the xy plane and that the vibrating mass element of the proposed micromechanical z-axis inertial sensor can be displaced in the z direction .
[0033] figure 1 A top view of a first embodiment of the proposed micromechanical z-axis inertial sensor 100 is shown.
[0034] An attachment element 30a can be seen, by means of which the first seismic mass element 10a is attached to the substrate 1 . In the event of an acceleration force acting on the first seismic mass element 10a, the first seismic mass element moves planarly downward or upward in the z-direction. Starting from the attachment element 30a, a first torsion spring element 11a can be seen, which can be twisted about the y-axis when the first seismic mass element 10a is offset parallel to the xy plane.
[0035] For the micromechanical z-ax...
PUM
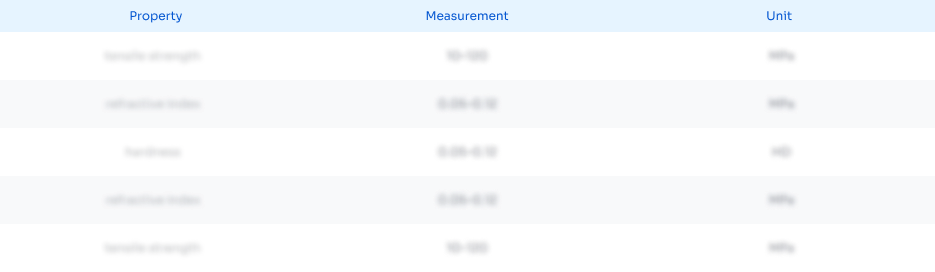
Abstract
Description
Claims
Application Information

- R&D
- Intellectual Property
- Life Sciences
- Materials
- Tech Scout
- Unparalleled Data Quality
- Higher Quality Content
- 60% Fewer Hallucinations
Browse by: Latest US Patents, China's latest patents, Technical Efficacy Thesaurus, Application Domain, Technology Topic, Popular Technical Reports.
© 2025 PatSnap. All rights reserved.Legal|Privacy policy|Modern Slavery Act Transparency Statement|Sitemap|About US| Contact US: help@patsnap.com