A Manipulator Structure Suitable for Warped Wafer Pick-and-Place
A technology of manipulators and wafers, which is applied in sustainable manufacturing/processing, climate sustainability, and final product manufacturing. It can solve the problems of easy falling and greater need for wafer adsorption, so as to achieve reliable bonding and prevent falling. Effect
- Summary
- Abstract
- Description
- Claims
- Application Information
AI Technical Summary
Problems solved by technology
Method used
Image
Examples
Embodiment 1
[0043] Example 1, as Figure 6-Figure 7 As shown, according to the actual size of the wafer, the distance between the two sets of positioning rods 206 is adjusted to ensure that the distance is consistent with the diameter of the wafer, and the two sets of second racks 207 are squeezed so that the second racks 207 are aligned with the first The racks 202 are separated from each other, and the two sets of support rods 209 are pushed to drive the slider 204 to slide inside the chute 201. Since the chute 201 is arranged obliquely on the bottom plate 1 of the manipulator, the two sets of positioning rods 206 are moved closer to or farther away from each other. , when adjusted to a proper position, loosen the second rack 207 under the elastic force of the first spring 208, and then engage and fix the second rack 207 with the first rack 202 again, so that the wafer can be positioned on the vacuum suction head 303 directly above the .
Embodiment 2
[0044] Example 2, as figure 1 , figure 2 , image 3 and Figure 9 As shown, when the wafer is placed on the manipulator base plate 1 at the same time, due to the serious warpage of the wafer surface and the multiple groups of vacuum suction heads 303 are far away from each other, at this time, the compressed air blowing plate 9 is driven by the micro cylinder 4 to the wafer. Move at the edge of the wafer, so that the compressed air port 903 moves to the edge of the wafer, and then the compressed air is delivered to the compressed air port 903 through the compressed air channel 904 through the compressed air line joint 8 through the blowing board, and the warpage Push the wafer to ensure that the wafer is attached to the manipulator base plate 1 to ensure reliable adsorption of the warped wafer. After completion, the micro cylinder 4 moves the compressed air blowing plate 9 to the original position to ensure that the compressed air blowing plate 9 for security.
[0045] Wo...
PUM
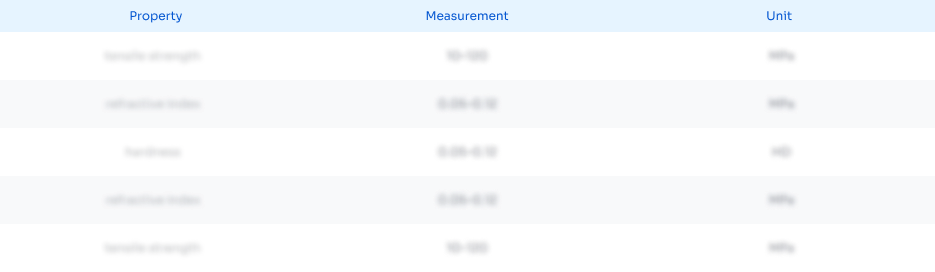
Abstract
Description
Claims
Application Information

- R&D
- Intellectual Property
- Life Sciences
- Materials
- Tech Scout
- Unparalleled Data Quality
- Higher Quality Content
- 60% Fewer Hallucinations
Browse by: Latest US Patents, China's latest patents, Technical Efficacy Thesaurus, Application Domain, Technology Topic, Popular Technical Reports.
© 2025 PatSnap. All rights reserved.Legal|Privacy policy|Modern Slavery Act Transparency Statement|Sitemap|About US| Contact US: help@patsnap.com