A method for measuring shield tail gap of shield machine based on dual-line laser vision
A shield tail gap and measurement method technology, applied in the direction of measuring devices, optical devices, instruments, etc., can solve the problems of low precision, data cannot be automatically saved and managed, laborious, etc., and achieve the effect of stable and reliable accuracy
- Summary
- Abstract
- Description
- Claims
- Application Information
AI Technical Summary
Problems solved by technology
Method used
Image
Examples
Embodiment 1
[0046] The invention provides a shield tail gap measurement method of a shield machine based on double-line laser vision, such as figure 1 shown, including:
[0047] Step 1: Collect the double-line laser return image to obtain the intersection of the feature lines of the double-line laser target;
[0048] Step 2: Use the intersection of the two-line laser target feature lines to obtain the shield tail gap distance of the shield machine.
[0049] Step 1 specifically includes:
[0050] 1-1: Use the double-line laser return image to extract the pixel point data of the double-line laser return image;
[0051]1-2: Use the pixel point data of the double-line laser to return the image to calculate the straight line equation of the double-line laser returned image based on the Hough line fitting algorithm;
[0052] 1-3: Calculate the intersection point of the feature line of the double-line laser target by using the straight line equation of the image returned by the double-line la...
Embodiment 2
[0082] The invention provides a shield tail gap measurement system of a shield machine based on double-line laser vision, such as figure 2 shown, including:
[0083] The acquisition module is used to collect the return image of the dual-line laser to obtain the intersection of the characteristic lines of the dual-line laser target;
[0084] The acquisition module is used to obtain the shield tail clearance distance of the shield machine by using the intersection of the two-line laser target feature lines.
Embodiment 3
[0086] The invention provides a practical application method for measuring the shield tail gap of a shield machine based on double-line laser vision, including:
[0087] The image processing algorithm is used to extract the two segment lines projected by the laser structure lines on the segment and the two shield lines on the shield tail shell in the image, and the pixel point information of the light spot is extracted, and the Hough line fitting algorithm is used to obtain the segment. Line and shield line effective spot slope and line equation, where the line equation of segment line and shield line are as follows:
[0088]
[0089] Among them, y is the y-axis coordinate value of the image pixel data returned by the dual-line laser, x is the x-axis coordinate value of the image pixel data returned by the dual-line laser, and k 管_1 is the straight line slope of the pixel point of the image returned by the laser of the first segment line, b 管_1 is the linear parameter of t...
PUM
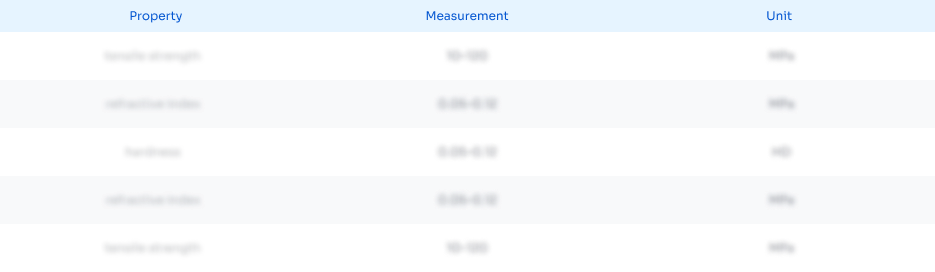
Abstract
Description
Claims
Application Information

- Generate Ideas
- Intellectual Property
- Life Sciences
- Materials
- Tech Scout
- Unparalleled Data Quality
- Higher Quality Content
- 60% Fewer Hallucinations
Browse by: Latest US Patents, China's latest patents, Technical Efficacy Thesaurus, Application Domain, Technology Topic, Popular Technical Reports.
© 2025 PatSnap. All rights reserved.Legal|Privacy policy|Modern Slavery Act Transparency Statement|Sitemap|About US| Contact US: help@patsnap.com