Flexible stirrup continuous feeding positioning machine and feeding positioning method
A positioning mechanism and stirrup technology, applied in auxiliary devices, applications, auxiliary welding equipment, etc., can solve the problems of inconvenient automatic production of stirrup cages, etc., and achieve the effect of simple structure, easy adjustment, and easy control
- Summary
- Abstract
- Description
- Claims
- Application Information
AI Technical Summary
Problems solved by technology
Method used
Image
Examples
Embodiment 1
[0036] See Figure 1 to Figure 8 , the flexible stirrup continuous feeding positioning machine of the present embodiment includes a control cabinet, an underframe, a left chain plate support mechanism and a right chain plate support mechanism arranged on the underframe, and the left chain plate support mechanism is provided with a The left alignment mechanism, the left pushing mechanism and the left positioning mechanism electrically connected to the control cabinet, the right chain plate supporting mechanism is provided with the right alignment mechanism, the right pushing mechanism and the right positioning mechanism electrically connected to the control cabinet, the The left alignment mechanism and the right alignment mechanism are used to align the stirrups left and right, the left pushing mechanism and the right pushing mechanism are used to push the stirrups, and the left positioning mechanism and the right positioning mechanism are used for Dual position front and rear ...
PUM
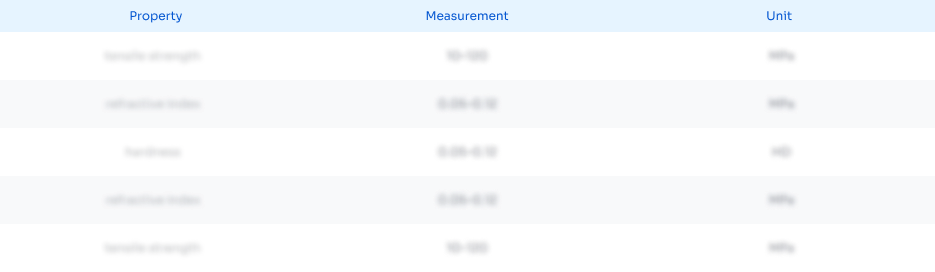
Abstract
Description
Claims
Application Information

- Generate Ideas
- Intellectual Property
- Life Sciences
- Materials
- Tech Scout
- Unparalleled Data Quality
- Higher Quality Content
- 60% Fewer Hallucinations
Browse by: Latest US Patents, China's latest patents, Technical Efficacy Thesaurus, Application Domain, Technology Topic, Popular Technical Reports.
© 2025 PatSnap. All rights reserved.Legal|Privacy policy|Modern Slavery Act Transparency Statement|Sitemap|About US| Contact US: help@patsnap.com