Method for reducing residual vibration of ultrasonic sensor, ultrasonic chip and ultrasonic device
An ultrasonic and sensor technology, applied in the field of ultrasonic chips and ultrasonic devices, can solve the problems of unpredictable, inability to fully compensate the sensor, blind compensation, etc., and achieve the effect of saving compensation time, flexible methods and flexible use.
- Summary
- Abstract
- Description
- Claims
- Application Information
AI Technical Summary
Problems solved by technology
Method used
Image
Examples
Embodiment 1
[0049] see Figure 3-Figure 4 As shown, a method for reducing the residual vibration of an ultrasonic sensor in this embodiment includes the following steps:
[0050] S1. Use the AD module to sample the amplitude of the first n sampling points of the aftershock of the ultrasonic sensor, where n is a natural number; then use the DA module to output a voltage value with the same amplitude but opposite phase to offset and compensate the first n sampling points; as a specific implementation, see Figure 3-Figure 4 As shown, use AD to sample the amplitude of the first n sampling points of aftershock (such as Figure 4 V1, V2, V3, V4, V5, V6, V7, V8), and then use DA to output voltage values with the same amplitude but opposite phase (ie -V1, -V2, -V3, -V4, -V5, -V6 , -V7, -V8) to offset and compensate the n sampling points;
[0051]S2. Use the AD module to sample the amplitude of the second n sampling points of the aftershock of the ultrasonic sensor, and then use the DA modul...
Embodiment 2
[0059] Corresponding to the method for reducing the residual vibration of the ultrasonic sensor in Embodiment 1, a corresponding ultrasonic chip for reducing the residual vibration of the ultrasonic sensor can be provided, and an AD module and a DA module are integrated in the ultrasonic chip.
[0060] Among them, the AD module is used to sample the amplitude of m times n sampling points of aftervibration of the ultrasonic sensor, wherein n is a natural number, and m is a natural number greater than 2.
[0061] The DA module is used to output voltage values with the same amplitude but opposite phases to offset and compensate n sampling points each time.
[0062] Use the AD module to sample the AD value of each point of the residual vibration, and then output the DA value of the same value but with the opposite phase at the corresponding position to offset the residual vibration. Every time a point is compensated, the AD value of the next point is scanned, and then the DA valu...
Embodiment 3
[0066] A method for reducing the residual vibration of an ultrasonic sensor in this embodiment includes the following steps:
[0067] After ADC sampling, directly control the DAC output signal with the same but opposite phase to the ultrasonic sensor.
[0068] Compared with Embodiment 1, this embodiment also has the advantages of easy implementation, obvious effects, flexible use, and low cost.
PUM
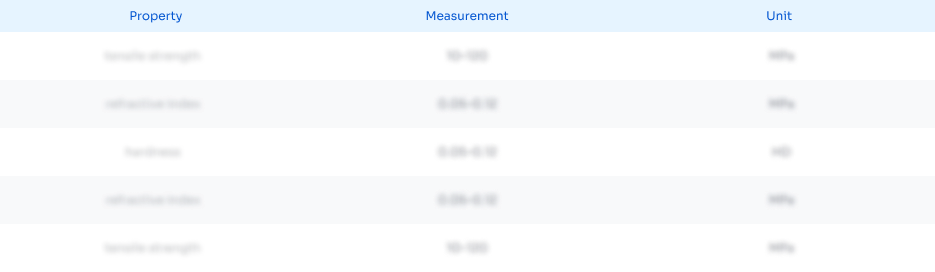
Abstract
Description
Claims
Application Information

- Generate Ideas
- Intellectual Property
- Life Sciences
- Materials
- Tech Scout
- Unparalleled Data Quality
- Higher Quality Content
- 60% Fewer Hallucinations
Browse by: Latest US Patents, China's latest patents, Technical Efficacy Thesaurus, Application Domain, Technology Topic, Popular Technical Reports.
© 2025 PatSnap. All rights reserved.Legal|Privacy policy|Modern Slavery Act Transparency Statement|Sitemap|About US| Contact US: help@patsnap.com