A high-response and large-range mems friction sensor
A sensor with a large range of technology, applied in the field of MEMS sensors, can solve the problems of inability to accurately measure the friction distribution of the aircraft surface, low sensitivity of the microbalance, and failure to meet the measurement requirements, etc., to achieve high frequency response, improve measurement sensitivity, and reliability high effect
- Summary
- Abstract
- Description
- Claims
- Application Information
AI Technical Summary
Problems solved by technology
Method used
Image
Examples
Embodiment 1
[0051] like figure 1 , figure 2 As shown, the high-response and large-range MEMS friction sensor of this embodiment includes a package cover 1 , a floating element 2 , a silicon microstructure 3 , an electrode substrate 4 , an interface circuit 5 and a package socket 6 . Wherein, the floating element 2 comprises a floating unit 9, a pole 10 and a positioning step 11, such as image 3 As shown; the silicon microstructure 3 includes a support frame 12, an elastic beam 13 and a vibrating plate 14, such as Figure 4 Shown; Electrode substrate 4 comprises lead electrode 15, metal electrode 16 and glass boss 17, as Figure 5 As shown; the vibrating plate 14 of the silicon microstructure 3 and the metal electrode 16 of the electrode substrate 4 form a differential sensitive capacitive element 18 to realize differential capacitance detection, as Image 6 As shown; the floating element 2, the silicon microstructure 3 and the electrode substrate 4 together constitute the head struc...
PUM
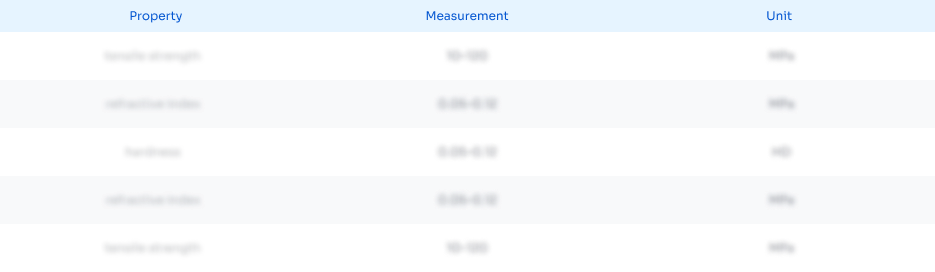
Abstract
Description
Claims
Application Information

- R&D Engineer
- R&D Manager
- IP Professional
- Industry Leading Data Capabilities
- Powerful AI technology
- Patent DNA Extraction
Browse by: Latest US Patents, China's latest patents, Technical Efficacy Thesaurus, Application Domain, Technology Topic, Popular Technical Reports.
© 2024 PatSnap. All rights reserved.Legal|Privacy policy|Modern Slavery Act Transparency Statement|Sitemap|About US| Contact US: help@patsnap.com