Control method of double-telescopic system
A control method and double telescopic technology, which are applied to the safety of the fluid pressure actuation system, the components of the fluid pressure actuation system, and the mechanism of the clockwork, etc., can solve the problem of errors in manual observation, increased manual workload, and damage to the telescopic arm structure. And other issues
- Summary
- Abstract
- Description
- Claims
- Application Information
AI Technical Summary
Problems solved by technology
Method used
Image
Examples
Embodiment Construction
[0058] The present invention will be described in further detail below in conjunction with the accompanying drawings and specific embodiments.
[0059] Such as Figure 1 to Figure 14 As shown, a control method of a double telescopic system, the control method is used to control the double telescopic system, the double telescopic system includes a hydraulic control system 1 and a double telescopic crane 2 (in Figure 11 shown in ), the hydraulic control system 1 includes a multi-way valve group 3, an oil tank 10, an oil pump 11, a hook limit valve group 4, an overload protection valve group 5 and a winch control module 12, and the oil tank 10 is connected to the oil pump 11 One end of the oil pump 11 is connected to the oil inlet end of the multi-way valve group 3, and the oil outlet end of the multi-way valve group 3 is connected to the oil tank 10; the hook limit valve group 4 is connected to the multi-way valve group 3 At the control end, an overload protection valve group ...
PUM
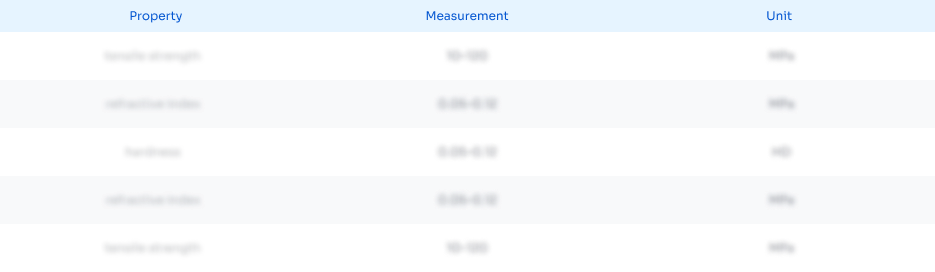
Abstract
Description
Claims
Application Information

- R&D Engineer
- R&D Manager
- IP Professional
- Industry Leading Data Capabilities
- Powerful AI technology
- Patent DNA Extraction
Browse by: Latest US Patents, China's latest patents, Technical Efficacy Thesaurus, Application Domain, Technology Topic, Popular Technical Reports.
© 2024 PatSnap. All rights reserved.Legal|Privacy policy|Modern Slavery Act Transparency Statement|Sitemap|About US| Contact US: help@patsnap.com