Ship crane optimization control method based on automatic gain tuning
An optimized control and automatic gain technology, applied in the direction of load hanging components, transportation and packaging, etc., can solve problems such as less consideration of system optimization control problems, no consideration of input saturation and state constraints, and many parameters, etc., to achieve improved optimal control effect of effect
- Summary
- Abstract
- Description
- Claims
- Application Information
AI Technical Summary
Problems solved by technology
Method used
Image
Examples
Embodiment 1
[0142] In this embodiment, the validity of the method of the present invention is verified through simulation and comparison with other methods. In this embodiment, the values of relevant parameters are as follows:
[0143] m B =10kg,m p =1.0kg,L B =0.9m, J=2.7kg·m 2 ,d=0.4m,g=9.8m / s 2 .
[0144] The initial value is ρ 1 (0)=5deg, ρ 2 (0)=0.10m, ρ 3 (0) = 0 deg.
[0145] The expected value is ρ 1d =60deg,ρ 2d =0.60m, ρ 3d = 0 degrees.
[0146] For the convenience of comparison, for the controller (abbreviated as TELC here), through trial and error, a more ideal control gain is obtained as k p1 =8.0,k p2 =15,k d1 =25,k d2 =15.
[0147] For the online gain adjustment controller based on model predictive control proposed by the present invention (abbreviated as MPCLCC here), the values of each weight matrix in the cost function (i.e. formula (a)) are respectively: Q=P=diag{10 4 10 4 10 4}, R={0.010.010.010.01}. The value ranges of the four control gains (...
PUM
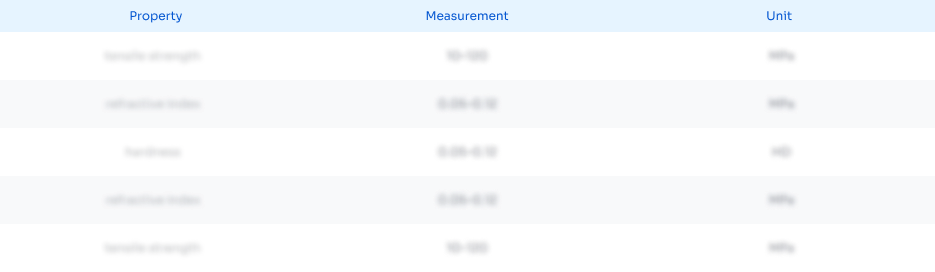
Abstract
Description
Claims
Application Information

- Generate Ideas
- Intellectual Property
- Life Sciences
- Materials
- Tech Scout
- Unparalleled Data Quality
- Higher Quality Content
- 60% Fewer Hallucinations
Browse by: Latest US Patents, China's latest patents, Technical Efficacy Thesaurus, Application Domain, Technology Topic, Popular Technical Reports.
© 2025 PatSnap. All rights reserved.Legal|Privacy policy|Modern Slavery Act Transparency Statement|Sitemap|About US| Contact US: help@patsnap.com