Variable working condition tool wear prediction method based on causal inference
A technology of tool wear and prediction method, applied in manufacturing tools, metal processing equipment, measuring/indicating equipment, etc., can solve the problems of information loss, affecting the accuracy of tool wear prediction, etc., to improve the prediction accuracy and reduce the effect of confounding effects
- Summary
- Abstract
- Description
- Claims
- Application Information
AI Technical Summary
Problems solved by technology
Method used
Image
Examples
Embodiment Construction
[0040] The present invention will be further described below in conjunction with accompanying drawings and examples.
[0041] Such as figure 1 -4 shown.
[0042] A tool wear prediction method based on causal inference, its flow chart is as follows figure 1 As shown, the specific steps are as follows:
[0043] Step 1. Collect and process the monitoring signals of the vibration sensor, current sensor and power sensor on the part and perform feature extraction, and at the same time collect and label the tool wear amount;
[0044] Step 2, signal feature extraction, mainly extracts the time domain, frequency domain, and time-frequency domain characteristics of the monitoring signal through statistical methods;
[0045] Step 3, signal feature optimization based on causal inference, mainly includes three parts: causal network establishment, causal effect calculation, and signal feature update; among them, the causal network establishment is shown in Figure 2 and Figure 3, and the ...
PUM
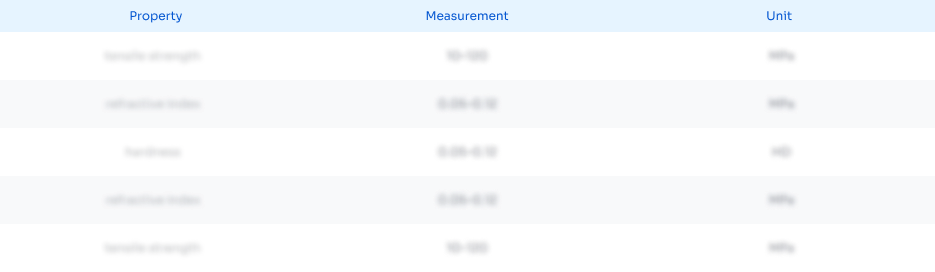
Abstract
Description
Claims
Application Information

- Generate Ideas
- Intellectual Property
- Life Sciences
- Materials
- Tech Scout
- Unparalleled Data Quality
- Higher Quality Content
- 60% Fewer Hallucinations
Browse by: Latest US Patents, China's latest patents, Technical Efficacy Thesaurus, Application Domain, Technology Topic, Popular Technical Reports.
© 2025 PatSnap. All rights reserved.Legal|Privacy policy|Modern Slavery Act Transparency Statement|Sitemap|About US| Contact US: help@patsnap.com