Iron core manufacturing process of motor for new energy automobile
A new energy vehicle and manufacturing process technology, which is applied in the manufacture of motor generators, stator/rotor bodies, electromechanical devices, etc., can solve the problems of poor concentricity of iron chips and poor dynamic balance of iron cores, and achieve good concentricity, Good dynamic balance to achieve lightweight effect
- Summary
- Abstract
- Description
- Claims
- Application Information
AI Technical Summary
Problems solved by technology
Method used
Image
Examples
Embodiment
[0025] Such as figure 1 with figure 2 As shown, the iron core manufacturing process of a new energy vehicle motor described in this embodiment includes the following steps:
[0026] In step S1, the material strip 100 is conveyed to the blanking direction in a continuous step-by-step manner between the upper die and the lower die of the continuous blanking die, wherein a continuous step is formed between the upper die and the lower die of the continuous blanking die. The continuous stepping punching station includes the first punching station 101 for punching the guide hole 3 and the forming hole, and the first punching station 101 for punching the ventilation hole 4 from the feeding to the blanking direction. The second punching station 102, the third punching station 103 for punching the first through hole 6, the fourth punching station for punching the first magnetic steel groove 9, the rotor buckle point 7 and the through hole 8 The punching station 104, the fifth punchi...
PUM
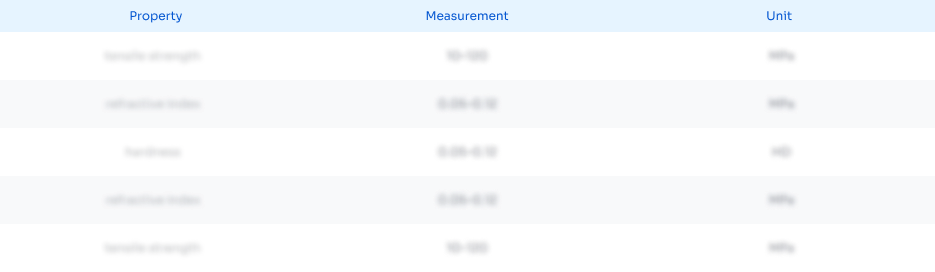
Abstract
Description
Claims
Application Information

- R&D
- Intellectual Property
- Life Sciences
- Materials
- Tech Scout
- Unparalleled Data Quality
- Higher Quality Content
- 60% Fewer Hallucinations
Browse by: Latest US Patents, China's latest patents, Technical Efficacy Thesaurus, Application Domain, Technology Topic, Popular Technical Reports.
© 2025 PatSnap. All rights reserved.Legal|Privacy policy|Modern Slavery Act Transparency Statement|Sitemap|About US| Contact US: help@patsnap.com