Friction energy harvesting self-powered monitoring system
A monitoring system and self-powered technology, which are applied in the field of ship turbulence amplitude and direction monitoring, ship positioning and tracking system, and shipborne wind direction monitoring. Single problem, to achieve the effect of high sensitivity, high reliability, simple structure and excitation process of direction measurement
- Summary
- Abstract
- Description
- Claims
- Application Information
AI Technical Summary
Problems solved by technology
Method used
Image
Examples
Embodiment Construction
[0030] A self-powered monitoring system for friction energy harvesting, which mainly includes a casing a, a base b, a torsion bar c, an excitation disc d, a sensor e, a disc spring k, a disc spring j, a moving disc h, a fixed disc i, a blunt Body m, streamer n, pressure plate o, circuit board p, sleeve r, guide column q, frequency modulation block s, outer ring pad f1, inner ring pad f2 and pressure ring f3.
[0031]The casing a is composed of the casing side wall a2 and the casing top wall a1, the inner side of the casing top wall a1 is provided with a ring platform a3, and the casing top wall a1 is provided with a ball cavity a4; the end of the casing side wall a2 is The screws are installed on the base b, and the base b crimps the outer edge of the fixed plate i to the ring platform a3 inside the top wall a1 of the casing through the outer ring pad f1. Between two adjacent fixed plates i, the fixed plate and the There are outer ring pads f1 between the base b and between th...
PUM
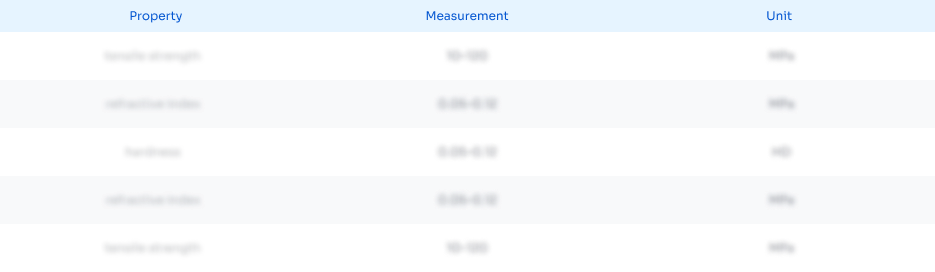
Abstract
Description
Claims
Application Information

- Generate Ideas
- Intellectual Property
- Life Sciences
- Materials
- Tech Scout
- Unparalleled Data Quality
- Higher Quality Content
- 60% Fewer Hallucinations
Browse by: Latest US Patents, China's latest patents, Technical Efficacy Thesaurus, Application Domain, Technology Topic, Popular Technical Reports.
© 2025 PatSnap. All rights reserved.Legal|Privacy policy|Modern Slavery Act Transparency Statement|Sitemap|About US| Contact US: help@patsnap.com