Mechanism-data fusion driven variable working condition tool wear state monitoring method
A tool wear and state technology, applied in the direction of manufacturing tools, metal processing equipment, measuring/indicating equipment, etc., can solve the problems of difficult installation of dynamometer, low monitoring accuracy, limited cost, etc.
- Summary
- Abstract
- Description
- Claims
- Application Information
AI Technical Summary
Problems solved by technology
Method used
Image
Examples
Example Embodiment
[0072] Example 1
[0073] Mechanism model and machining data fusion tool wear condition monitoring method, such as figure 2 As shown, including the following steps:
[0074] Step 1) Synchronize the spindle vibration signal, current signal, and NC command data, the NC command data includes a tool name and milling parameters;
[0075] Step 2) Take the tool tag for the main shaft vibration signal and the spindle motor current signal of the tool different milling time in the tool name, the milling parameters, respectively;
[0076] Step 3) Access the spindle acceleration and the spindle motor current signal, based on the spindle acceleration and the spindle motor current signal reconstruction milling force, further calculate the milling force coefficient;
[0077] Step 4) Based on the milling force coefficient, the regression model is established by depth learning, based on the regression model, the tool wear status identification and the remaining life prediction;
[0078] Step 5) Ge...
Example Embodiment
[0080] Example 2
[0081] Combine figure 1 and figure 2, By the acceleration sensor attached to the main shaft near the shank position, the spindle vibration signal is collected, the spindle motor current signal (obvious to the electric spindle effect) is collected by a low-pass filter processing reconstruction milling force. . The key steps are as follows: The key steps are as follows:
[0082] Step (1): Data Synchronous Collection: By acceleration signal, current signal reconstruct the milling force, and thus linear regression is obtained by the milling force coefficient. It is necessary to implement machine tool external sensor data synchronous acquisition, and sensor data includes spindle vibration signals, current signals, NC command data refers to spindle rotation speed, feed speed, X / Y / Z axis coordinate, tool teeth, tool name, etc. information. The external sensor data collects through the data acquisition system, and the NC command data reads from the Siemens CNC syste...
Example Embodiment
[0126] Example 3
[0127] Mechanism model and machining data fusion tool wear condition monitoring system, including:
[0128] The data acquisition unit is used to synchronize the spindle vibration signal, current signal, and NC command data;
[0129] The time series correspondence unit, intersecting the data acquisition unit, for use in a tool name, milling parameter as a label, respectively, the main shaft vibration signal and the current signal of the tool different milling time, respectively;
[0130] The milling force reconstruction unit is interspersed with the time series corresponding unit to acquire the spindle acceleration and the spindle motor current signal. Based on the spindle acceleration and the spindle motor current signal reconstruction milling force, the milling force coefficient is further calculated, and the milling force coefficient Identify.
[0131] Wear state identification unit, intersecting the milling force reconstruction unit, for use in milling force ...
PUM
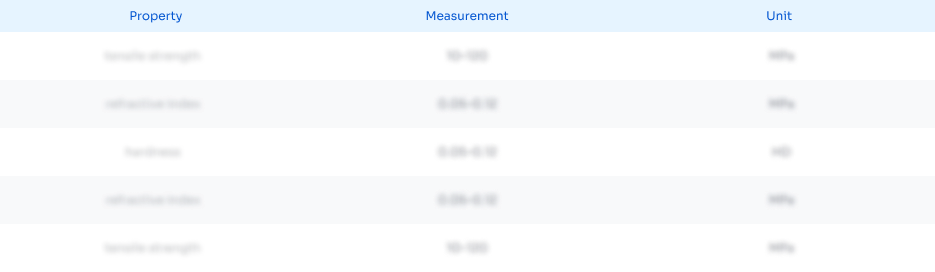
Abstract
Description
Claims
Application Information

- Generate Ideas
- Intellectual Property
- Life Sciences
- Materials
- Tech Scout
- Unparalleled Data Quality
- Higher Quality Content
- 60% Fewer Hallucinations
Browse by: Latest US Patents, China's latest patents, Technical Efficacy Thesaurus, Application Domain, Technology Topic, Popular Technical Reports.
© 2025 PatSnap. All rights reserved.Legal|Privacy policy|Modern Slavery Act Transparency Statement|Sitemap|About US| Contact US: help@patsnap.com