Multi-directional locking device for automatic lift of civil aircraft containerized cargo system
A civil aircraft, automatic lift technology, applied in the direction of equipment for loading and unloading goods, aircraft parts, building locks, etc., can solve problems such as inability to meet
- Summary
- Abstract
- Description
- Claims
- Application Information
AI Technical Summary
Problems solved by technology
Method used
Image
Examples
Embodiment Construction
[0032] The present application will be further described in detail below through specific embodiments and accompanying drawings.
[0033] The multi-directional locking device for the automatic lift of the containerized cargo system of the civil aircraft provided by the present invention includes: a locking bolt 1, a base 6, a linkage rod 2, a limiting arm 4 and an unlocking arm 8,
[0034] The locking tongue 1 is located on the left side of the base 6 , and the locking tongue 1 and the base 6 are connected by a hinge. The linkage rod 2 is located in the middle of the locking bolt 1 , and the two ends of the linkage rod 2 are hingedly connected to the locking bolt 1 respectively.
[0035] In the present invention, the locking bolt 1 has four limit surfaces, wherein the vertical limit surface 15 is located above the lock bolt, the course limit surface 14 and the reverse course limit surface 17 are located on both sides of the vertical limit surface 15, The lateral limit surface...
PUM
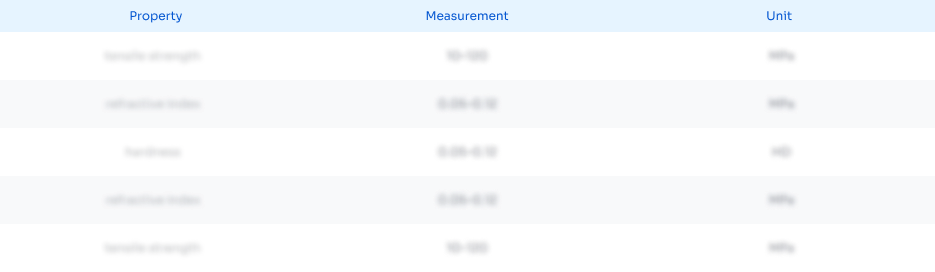
Abstract
Description
Claims
Application Information

- Generate Ideas
- Intellectual Property
- Life Sciences
- Materials
- Tech Scout
- Unparalleled Data Quality
- Higher Quality Content
- 60% Fewer Hallucinations
Browse by: Latest US Patents, China's latest patents, Technical Efficacy Thesaurus, Application Domain, Technology Topic, Popular Technical Reports.
© 2025 PatSnap. All rights reserved.Legal|Privacy policy|Modern Slavery Act Transparency Statement|Sitemap|About US| Contact US: help@patsnap.com