Preparation method of modified polypropylene melt-blown filter element
A technology of polypropylene melt-blown and polypropylene, applied in chemical instruments and methods, filtration treatment, adsorption water/sewage treatment, etc., can solve problems such as poor uniformity and stability, complex preparation process, and loss of adsorbents. Achieve stable removal effect, simple preparation process, and reduce waste liquid discharge
- Summary
- Abstract
- Description
- Claims
- Application Information
AI Technical Summary
Problems solved by technology
Method used
Examples
Embodiment 1
[0015] Example 1: Mix 80 parts of polypropylene with 20 parts of styrene-maleic anhydride copolymer, pour them into a barrel, extrude the raw materials through an extruder, and draw and stretch them under hot air at 250°C. The wire is then wound and cut on the receiving rod to form a polypropylene melt-blown filter element. Then place the filter element in a water-methanol (volume ratio 1:1) solution of 5wt% polyethyleneimine, react at 90°C for 12h, wash and dry to obtain a modified polypropylene filter element, at pH=7 Under the conditions, its removal rate of 25ppb cadmium ions is 99%.
Embodiment 2
[0016] Example 2: Mix 70 parts of polypropylene with 20 parts of styrene-maleic anhydride and 10 parts of polypropylene-maleic anhydride copolymer, pour it into the barrel, extrude the raw materials through an extruder, and The filaments are stretched under hot air at 300°C, and then wound and cut on a receiving rod to form polypropylene melt-blown filter elements. Then place the filter element in a 3wt% aqueous solution of ethylenediamine, react at 65°C for 18h, wash and dry to obtain a modified polypropylene filter element, and under the condition of pH=7, it can remove 25ppb of cadmium ions The rate is 96%.
Embodiment 3
[0017] Example 3: Mix 90 parts of polypropylene with 10 parts of polypropylene-styrene-maleic anhydride copolymer, pour it into a barrel, extrude the raw material through an extruder, and draw it under hot air at 240°C It is stretched into filaments, then wound on a receiving rod and cut to form a polypropylene meltblown filter element. Then place the filter element in a solution of 10wt% piperazine in water-ethanol (volume ratio 2:1), react at 70°C for 15h, wash and dry to obtain a modified polypropylene filter element, under the condition of pH=7 , its removal rate to 25ppb cadmium ions is 92%.
PUM
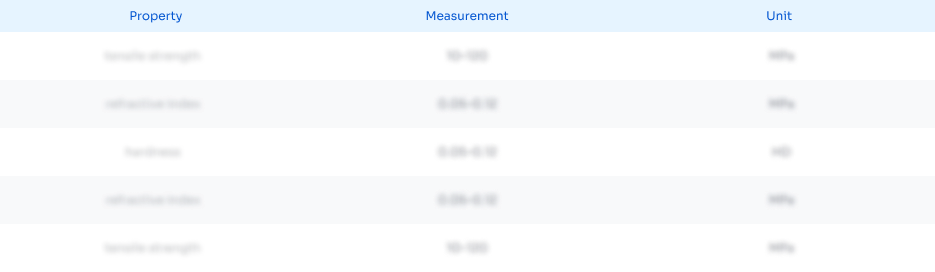
Abstract
Description
Claims
Application Information

- Generate Ideas
- Intellectual Property
- Life Sciences
- Materials
- Tech Scout
- Unparalleled Data Quality
- Higher Quality Content
- 60% Fewer Hallucinations
Browse by: Latest US Patents, China's latest patents, Technical Efficacy Thesaurus, Application Domain, Technology Topic, Popular Technical Reports.
© 2025 PatSnap. All rights reserved.Legal|Privacy policy|Modern Slavery Act Transparency Statement|Sitemap|About US| Contact US: help@patsnap.com