High-frequency sensor and manufacturing method thereof
A high-frequency sensor and sensor technology, applied in the field of sensors, can solve the problems of short time for returning echo signals, affecting the accuracy of ranging, and achieve the effects of improving accuracy, reducing cumbersome installation steps, and enhancing strength
- Summary
- Abstract
- Description
- Claims
- Application Information
AI Technical Summary
Problems solved by technology
Method used
Image
Examples
Embodiment 1
[0045] A high-frequency sensor, comprising a shell, a first matching layer, a PCB circuit board, a piezoelectric ceramic sheet and a second matching layer, the first matching layer, a PCB circuit board, a piezoelectric ceramic sheet and the second matching layer are arranged on the shell In the body, one side of the first matching layer is in contact with the housing, the other side of the first matching layer is in contact with the upper surface of the PCB circuit board, and the lower surface of the PCB circuit board is in contact with the upper surface of the piezoelectric ceramic sheet. The lower surface of the sheet is in close contact with the second matching layer, the other side of the second matching layer is used to transmit ultrasonic signals outward, and the connection between the other side of the second matching layer and the housing has an arc structure. The vibration-damping glue layer is also included, and the vibration-damping glue layer is arranged on the outs...
Embodiment 2
[0060] In the method for making a high-frequency sensor, the arc of the arc structure 12 is completed in the following manner:
[0061] A) Put the semi-finished sensor with the glue injection side up into the dispensing tool, set the dispensing time and dispensing air pressure of the dispensing machine, and use the No. 6 needle in the glue layer on the side Apply a layer of primer first, and keep the glue between 3-5mm from the upper surface. The schematic diagram of the sensor placed with the glue injection side up is as follows: Figure 9 shown. The upper end surface refers to a plane that is flat with the surface of the second matching layer that is used to transmit ultrasonic signals to the outside.
[0062] B) Place the glued product in a 60-degree oven for 1 hour to dry;
[0063] C) Then apply a layer of glue on the entire surface of the product, keep the upper surface of the glue flat with the upper end surface, and then wipe off the excess glue. Or use the method o...
PUM
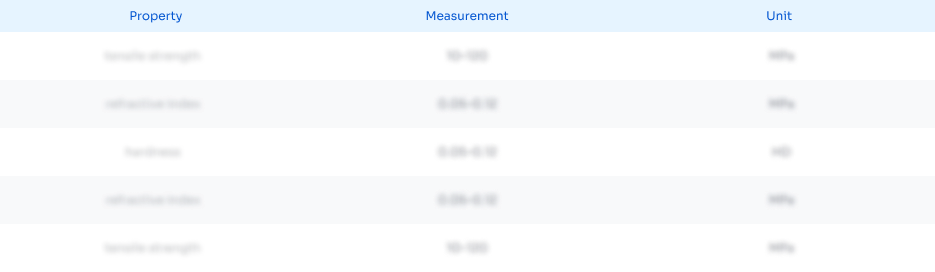
Abstract
Description
Claims
Application Information

- R&D
- Intellectual Property
- Life Sciences
- Materials
- Tech Scout
- Unparalleled Data Quality
- Higher Quality Content
- 60% Fewer Hallucinations
Browse by: Latest US Patents, China's latest patents, Technical Efficacy Thesaurus, Application Domain, Technology Topic, Popular Technical Reports.
© 2025 PatSnap. All rights reserved.Legal|Privacy policy|Modern Slavery Act Transparency Statement|Sitemap|About US| Contact US: help@patsnap.com