Beam dyeing and rolling process
A warp beam dyeing and process technology, applied in the field of warp beam dyeing technology, can solve problems such as affecting product quality and production progress, damage to the white edge of the mesh cylinder, etc., to avoid relative slippage, avoid wood grain damage, and uniform resistance.
- Summary
- Abstract
- Description
- Claims
- Application Information
AI Technical Summary
Problems solved by technology
Method used
Image
Examples
Embodiment 1~13
[0031] Refer to attached figure 1 : A warp beam dyeing and rolling process, in which a single weight 1kg weight 3 is hung at both ends of the tension shaft 1 of the warp beam rolling machine to increase the rolling tension of the cloth roll 2, and when rolling 15~25m and Subsequent rolling will reduce the counterweight by 1~2kg after every 12~17m of rolling, until the additional counterweight is 0. And at the beginning of rolling the cloth roll 2, the front end of the cloth is sewed with 1.5m of real silk satin of the same fabric as the cloth, and then sewed with 2m of cotton guide cloth, and rolled from the guide cloth to the net cylinder. The specific parameters of each embodiment are as follows Table 1.
[0032] Wherein, the external tension is to hang 1 kg of pendant 3 as evenly as possible at both ends of the tension shaft 1 to the required tension, and in the case of an odd number, one more pendant 3 can be hung at either end.
[0033] Table 1 Rolling parameters
[00...
PUM
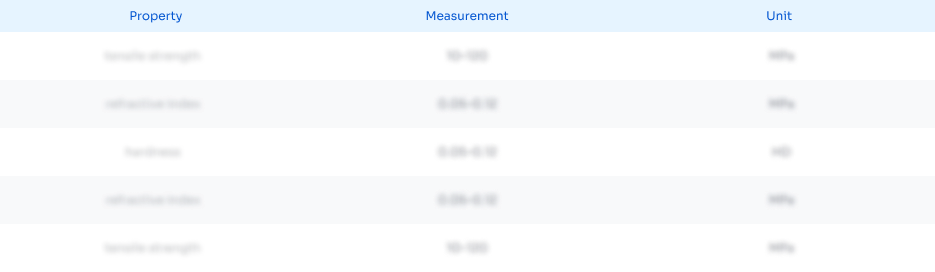
Abstract
Description
Claims
Application Information

- Generate Ideas
- Intellectual Property
- Life Sciences
- Materials
- Tech Scout
- Unparalleled Data Quality
- Higher Quality Content
- 60% Fewer Hallucinations
Browse by: Latest US Patents, China's latest patents, Technical Efficacy Thesaurus, Application Domain, Technology Topic, Popular Technical Reports.
© 2025 PatSnap. All rights reserved.Legal|Privacy policy|Modern Slavery Act Transparency Statement|Sitemap|About US| Contact US: help@patsnap.com