Coal-pillar-free self-forming roadway balanced mining design method and system
A design method and technology without coal pillars, applied in mining equipment, surface mining, earthwork drilling, etc., can solve the problems of design limitations, inability to scientifically and effectively compensate for the stress loss of the roadway facing surface, etc.
- Summary
- Abstract
- Description
- Claims
- Application Information
AI Technical Summary
Problems solved by technology
Method used
Image
Examples
Embodiment 1
[0030] This embodiment provides a method for designing balanced mining of self-formed roadways without coal pillars, including:
[0031] Using the rock mass disintegration function equation, the rock mass disintegration coefficient is obtained;
[0032] Based on the rock mass disintegration coefficient, using the stope distension control equation, the top cut height that makes the stope reach the disintegration balance is obtained;
[0033] Using a series of indoor tests to obtain the coefficient of the cut surface, and compare the friction force of the cut surface to obtain the roof cut angle when the roof collapse resistance of the stope is the smallest;
[0034] Obtain the support balance parameters of the self-forming roadway, verify the top cutting height, the top cutting angle and the self-forming roadway support balance parameters, obtain the balanced mining design parameters, and finally form the balanced mining plan of the self-forming roadway without coal pillars.
...
Embodiment 2
[0053] This embodiment provides a balanced mining design system for self-forming roadways without coal pillars, including:
[0054] The rock mass disintegration coefficient calculation module is used to obtain the rock mass disintegration coefficient by using the rock mass disintegration function equation;
[0055] The roof cutting height calculation module is used to obtain the roof cutting height for the stope to reach the breaking and swelling balance based on the rock mass breaking coefficient and using the stope breaking expansion control equation;
[0056] The roof cutting angle calculation module is used to obtain the friction coefficient between the roof strata, and the roof cutting angle when the roof caving resistance of the stope is the smallest is obtained by comparing the friction force of the cut surface;
[0057] Mining plan formation module, which is used to obtain the support balance parameters of the self-forming roadway, verify the top cutting height, angle ...
PUM
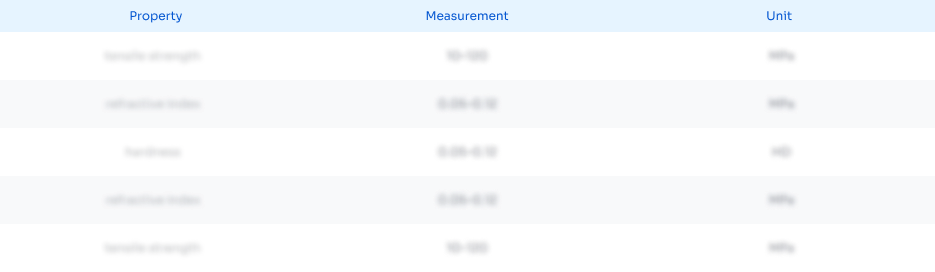
Abstract
Description
Claims
Application Information

- Generate Ideas
- Intellectual Property
- Life Sciences
- Materials
- Tech Scout
- Unparalleled Data Quality
- Higher Quality Content
- 60% Fewer Hallucinations
Browse by: Latest US Patents, China's latest patents, Technical Efficacy Thesaurus, Application Domain, Technology Topic, Popular Technical Reports.
© 2025 PatSnap. All rights reserved.Legal|Privacy policy|Modern Slavery Act Transparency Statement|Sitemap|About US| Contact US: help@patsnap.com