A self-balancing maglev rotor system based on same-frequency displacement adaptive filtering
A magnetic levitation rotor and self-adaptive filter technology, applied in self-adaptive control, general control system, control/adjustment system, etc., can solve the problems affecting the accuracy of automatic balance, achieve the effects of offsetting adverse effects, simple algorithm, and improving suppression accuracy
- Summary
- Abstract
- Description
- Claims
- Application Information
AI Technical Summary
Problems solved by technology
Method used
Image
Examples
Embodiment Construction
[0026] The present invention will be further described below with reference to the drawings and specific embodiments.
[0027] Magnetic suspension rotor such as figure 1 Shown. Π 1 , Π 2 Are the center planes of radial magnetic bearing electromagnets A and B respectively, Π is the center plane of the rotor, the rotor inertial main axis and Π 1 , Π 2 And Π are handed to C respectively 1 , C 2 And C, rotor geometry axis and Π 1 , Π 2 And Π are handed to O 1 , O 2 And O, the line between the stator centers of electromagnet A and B intersects with Π at N. Magnetic suspension rotor center plane Π such as figure 2 Shown. In Π, a fixed coordinate system NXY relative to the inertial space is established with N as the origin, and a rotating coordinate system Oεη rotating with the rotor speed Ω is established with O as the origin. OC, O 1 C 1 , O 2 C 2 The lengths of are l, m, n, the angle between OC and Oε coordinate axis is θ, O 1 C 1 , O 2 C 2 The angles between the projected Π and th...
PUM
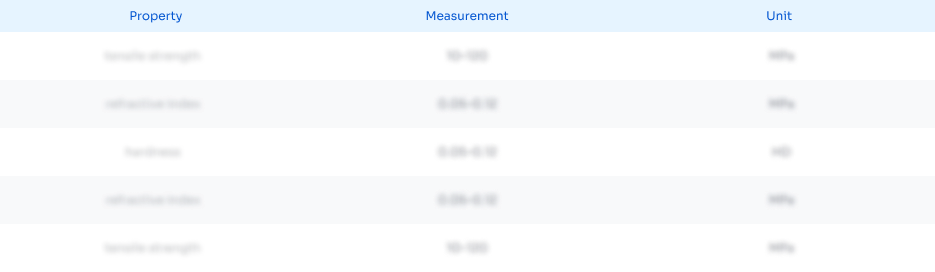
Abstract
Description
Claims
Application Information

- R&D
- Intellectual Property
- Life Sciences
- Materials
- Tech Scout
- Unparalleled Data Quality
- Higher Quality Content
- 60% Fewer Hallucinations
Browse by: Latest US Patents, China's latest patents, Technical Efficacy Thesaurus, Application Domain, Technology Topic, Popular Technical Reports.
© 2025 PatSnap. All rights reserved.Legal|Privacy policy|Modern Slavery Act Transparency Statement|Sitemap|About US| Contact US: help@patsnap.com