Anti-skid control system and method for grabbing manipulator
A technology for grasping manipulators and control systems, applied in manipulators, program-controlled manipulators, manufacturing tools, etc., can solve problems such as poor anti-skid performance of grasping manipulators, achieve the effect of improving grasping accuracy and reducing slippage
- Summary
- Abstract
- Description
- Claims
- Application Information
AI Technical Summary
Problems solved by technology
Method used
Image
Examples
Embodiment 1
[0026] Such as figure 1 As shown, an anti-skid control system for a grasping manipulator is composed of a slip sensor, a signal conditioning circuit, an upper computer PC, a single-chip microcomputer, and a driving motor. The slip sensor is installed on the grasping manipulator, and the slip sensor is connected to the signal conditioning circuit. The computer PC is connected with the signal conditioning circuit, and the single-chip microcomputer system is respectively connected with the upper computer PC and the driving motor electromechanically. The anti-skid control system of the grasping manipulator adjusts the grasping force according to the pressure detected by the sensor, and then according to the information obtained by the feedback system, so as to realize the grasping of objects of different materials with different strengths.
[0027] The slip sensor preferably used in the present invention is a piezoresistive sensor. Compared with the piezoelectric sensor, the piezo...
Embodiment 2
[0030] The present invention also provides a grasping manipulator, which adopts the anti-slip control system of the grasping manipulator for anti-slip control. While effectively improving the grasping accuracy of the manipulator, the slippage of the manipulator during the grasping operation is reduced.
Embodiment 3
[0032] The embodiment of the present invention provides a control method for the anti-skid control system of the grasping manipulator, the specific process is as follows image 3 As shown, the specific steps are as follows: the grasping manipulator realizes grasping through the steering gear; the sliding force is generated when grasping; the sliding sensor detects the sliding signal; the upper computer PC converts the force signal into a digital signal through the signal conditioning circuit; the single-chip microcomputer accepts the digital signal signal to control the servo to adjust the clamping force; the clamping is completed after eliminating the slippage. The whole control process adjusts the grasping force according to the pressure detected by the slip sensor, and then adjusts the grasping force according to the information obtained by the feedback system, so as to realize the grasping of objects of different materials with different strengths, effectively reducing the ...
PUM
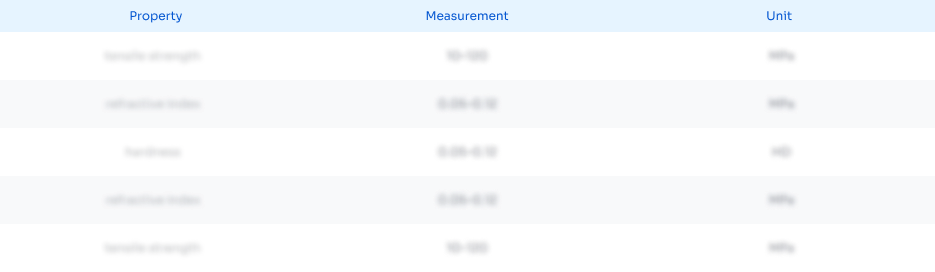
Abstract
Description
Claims
Application Information

- R&D
- Intellectual Property
- Life Sciences
- Materials
- Tech Scout
- Unparalleled Data Quality
- Higher Quality Content
- 60% Fewer Hallucinations
Browse by: Latest US Patents, China's latest patents, Technical Efficacy Thesaurus, Application Domain, Technology Topic, Popular Technical Reports.
© 2025 PatSnap. All rights reserved.Legal|Privacy policy|Modern Slavery Act Transparency Statement|Sitemap|About US| Contact US: help@patsnap.com