Fabricated outer wall based on lightweight outer wall enclosure plates
A kind of enclosure, prefabricated technology, used in walls, building components, thermal insulation and other directions, can solve the problems of complex construction, unsatisfactory, long construction period, etc., to improve the connection strength and compactness, prevent relative displacement and deformation, Meet the effect of wind resistance
- Summary
- Abstract
- Description
- Claims
- Application Information
AI Technical Summary
Problems solved by technology
Method used
Image
Examples
Embodiment 1
[0027] Example 1: See Figure 1 to Figure 5 , a prefabricated exterior wall based on lightweight exterior wall panels, the prefabricated exterior wall is spliced by several lightweight exterior wall panels 1, and the exterior wall panels include light concrete cement-based building materials ( For example, the outer leaf plate 1-1 and the inner leaf plate 1-2 made by foaming cement) foaming, and the thermal insulation layer 1-3 bonded between the outer leaf plate and the inner leaf plate; the thermal insulation layer can adopt the prior art Made of building insulation materials, such as polystyrene boards; the thickness of the outer blades is less than or equal to the thickness of the inner blades. The specific thickness can be designed according to the actual building requirements. The present invention adopts composite technology to carry out composite molding of the heat preservation board and the inner and outer leaf boards to ensure the connectivity of the heat preserv...
Embodiment 2
[0030] Example 2, see Image 6 , steel mesh 1-6 is arranged inside the outer leaf plate and the inner leaf plate. Improve the compression and bending resistance of the board body, and improve the safety of use.
Embodiment 3
[0031] Example 3, see Figure 7 , the steel mesh in the outer leaf plate and the inner leaf plate is provided with tie bars 1-7, and the tie bars pass through the insulation layer to form a built-in steel skeleton structure. The steel bar skeleton formed by the above combination can also be Reinforced truss structure. Further improve its compressive and flexural resistance, and connect the inner and outer blades into a stressed whole through the steel skeleton, so that it can bear greater wind pressure and earthquake resistance.
PUM
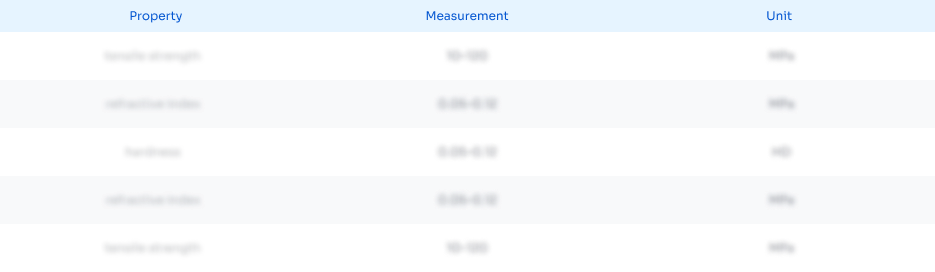
Abstract
Description
Claims
Application Information

- R&D Engineer
- R&D Manager
- IP Professional
- Industry Leading Data Capabilities
- Powerful AI technology
- Patent DNA Extraction
Browse by: Latest US Patents, China's latest patents, Technical Efficacy Thesaurus, Application Domain, Technology Topic, Popular Technical Reports.
© 2024 PatSnap. All rights reserved.Legal|Privacy policy|Modern Slavery Act Transparency Statement|Sitemap|About US| Contact US: help@patsnap.com