Part cooling-rim sealing structure for step-by-step utilization of cooling airflow of gas turbine
A technology for cooling airflow and gas turbines, which is applied in the cooling of engines, turbines/propulsion devices, and engine components, etc. It can solve the problems of reducing turbine efficiency, cooling airflow loss, and increasing fuel consumption, achieving both safety and reduction Effect of cooling airflow loss and gap reduction
- Summary
- Abstract
- Description
- Claims
- Application Information
AI Technical Summary
Problems solved by technology
Method used
Image
Examples
Embodiment Construction
[0028] The embodiments of the present invention will be described in detail below in conjunction with the accompanying drawings. This embodiment is based on the technical solution of the present invention, and provides detailed implementation methods and specific operating procedures, but the scope of protection of the present invention is not limited to the following embodiments. .
[0029] see figure 1 and figure 2 , a component cooling-rim sealing structure for the gas turbine cooling airflow to be utilized step by step provided by the present invention, including the stationary blade 2 and its stationary blade platform 5, the front stage moving blade 1 and the front stage moving blade disc 4, and the rear stage moving blade 3 and the latter stage moving blade disc 6, sealed stator 8, sealed rotor 9, and rotating shaft 11. The front-stage rotor blade 1 is connected to the front-stage rotor blade disc 4 through a blade root-rim structure, the front-stage rotor blade disc ...
PUM
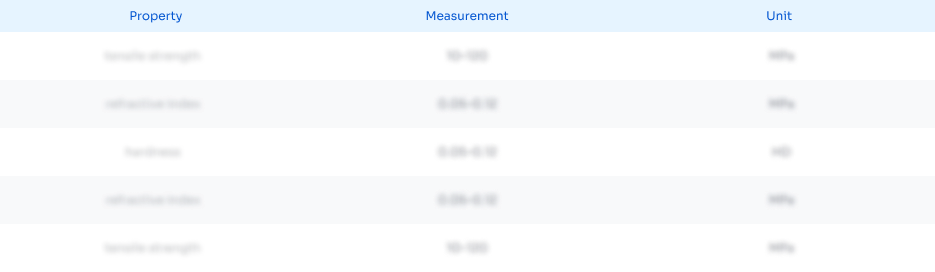
Abstract
Description
Claims
Application Information

- Generate Ideas
- Intellectual Property
- Life Sciences
- Materials
- Tech Scout
- Unparalleled Data Quality
- Higher Quality Content
- 60% Fewer Hallucinations
Browse by: Latest US Patents, China's latest patents, Technical Efficacy Thesaurus, Application Domain, Technology Topic, Popular Technical Reports.
© 2025 PatSnap. All rights reserved.Legal|Privacy policy|Modern Slavery Act Transparency Statement|Sitemap|About US| Contact US: help@patsnap.com