Blade structure for reducing noise and air loss of hydraulic retarder
A hydraulic retarder and blade structure technology, applied in the direction of liquid resistance brakes, brake components, noise/vibration control, etc., can solve the noise problems of vehicle drivers and residents around the road, increase vehicle fuel consumption, energy loss, etc. problem, to achieve the effect of improving driving safety, reducing interference and reducing noise
- Summary
- Abstract
- Description
- Claims
- Application Information
AI Technical Summary
Problems solved by technology
Method used
Image
Examples
Embodiment 1
[0022] see Figure 1 to Figure 5 , the present invention provides a technical solution: a blade structure for reducing noise and air loss of a hydraulic retarder, including a stator 1 and a rotor 2, the stator 1 is located on one side of the rotor 2, and the inner side of the stator 1 and the rotor 2 is provided with The blades 3, the blades 3 in the stator 1 and the rotor 2 are all arranged in a circular array, and the edge of one end of the blade 3 is fixed with a saw-toothed bar 4, and the designed saw-toothed bar 4 is installed on the blade 3, thereby realizing the Changing the tooth shape of rotor 2 and stator 1 has the effect of reducing noise and drag. There are tooth grooves on the sawtooth bar 4, and the tooth grooves are located on the sawtooth bar 4 in a half-sine wave. The cogging on the top is set with sine wave fluctuations, thereby ensuring that the sawtooth bar 4 changes the eddy current intensity in the working chamber of the rotor 2 and the stator 1, which ca...
Embodiment 2
[0026] see Figure 1 to Figure 5 , the present invention provides a technical solution: a blade structure for reducing noise and air loss of a hydraulic retarder, including a stator 1 and a rotor 2, the stator 1 is located on one side of the rotor 2, and the inner side of the stator 1 and the rotor 2 is provided with The blades 3, the blades 3 in the stator 1 and the rotor 2 are all arranged in a circular array, and the edge of one end of the blade 3 is fixed with a saw-toothed bar 4, and the designed saw-toothed bar 4 is installed on the blade 3, thereby realizing the Changing the tooth shape of rotor 2 and stator 1 has the effect of reducing noise and drag. There are tooth grooves on the sawtooth bar 4, and the tooth grooves are located on the sawtooth bar 4 in a half-sine wave. The cogging on the top is set with sine wave fluctuations, thereby ensuring that the sawtooth bar 4 changes the eddy current intensity in the working chamber of the rotor 2 and the stator 1, which ca...
Embodiment 3
[0030] see Figure 1 to Figure 5, the present invention provides a technical solution: a blade structure for reducing noise and air loss of a hydraulic retarder, including a stator 1 and a rotor 2, the stator 1 is located on one side of the rotor 2, and the inner side of the stator 1 and the rotor 2 is provided with The blades 3, the blades 3 in the stator 1 and the rotor 2 are all arranged in a circular array, and the edge of one end of the blade 3 is fixed with a saw-toothed bar 4, and the designed saw-toothed bar 4 is installed on the blade 3, thereby realizing the Changing the tooth shape of rotor 2 and stator 1 has the effect of reducing noise and drag. There are tooth grooves on the sawtooth bar 4, and the tooth grooves are located on the sawtooth bar 4 in a half-sine wave. The cogging on the top is set with sine wave fluctuations, thereby ensuring that the sawtooth bar 4 changes the eddy current intensity in the working chamber of the rotor 2 and the stator 1, which can...
PUM
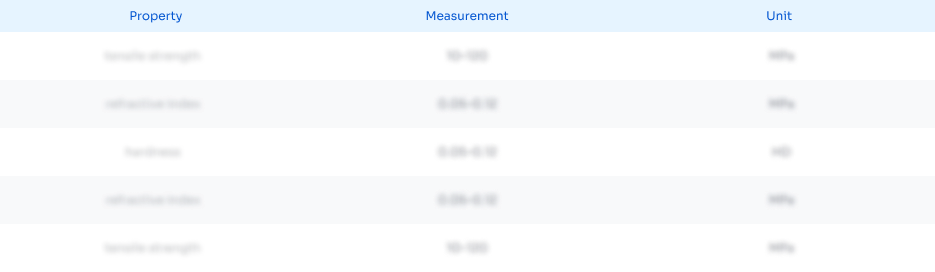
Abstract
Description
Claims
Application Information

- Generate Ideas
- Intellectual Property
- Life Sciences
- Materials
- Tech Scout
- Unparalleled Data Quality
- Higher Quality Content
- 60% Fewer Hallucinations
Browse by: Latest US Patents, China's latest patents, Technical Efficacy Thesaurus, Application Domain, Technology Topic, Popular Technical Reports.
© 2025 PatSnap. All rights reserved.Legal|Privacy policy|Modern Slavery Act Transparency Statement|Sitemap|About US| Contact US: help@patsnap.com