Multi-axis numerical control mechanical claw based on parallel mechanism
A mechanical claw and parallel technology, which is applied in the field of mechanical claws, can solve the problems of small grasping range of the manipulator and the grasping work of mechanical claws with lubrication failure, and achieve the effect of increasing the operable range, improving the sensitivity of use, and improving the efficiency of use
- Summary
- Abstract
- Description
- Claims
- Application Information
AI Technical Summary
Problems solved by technology
Method used
Image
Examples
Embodiment Construction
[0032] In order to make the technical means, creative features, goals and effects achieved by the present invention easy to understand, the present invention will be further described below in conjunction with specific embodiments.
[0033] Such as Figure 1-Figure 10 As shown, a multi-axis numerically controlled mechanical gripper based on a parallel mechanism in the present invention includes a grasping structure 1, a parallel rotating structure 2 and a packaging shell 5, and the bottom of the parallel rotating structure 2 is rotatably connected to the packaging shell 5, so There is a mechanical claw angle adjustment cavity 51 inside the packaging shell 5;
[0034]The grasping structure 1 includes a first fixed plate 11, a first rotating rod 12, a second rotating rod 13, a second fixed plate 14, a third rotating rod 15, a clamping plate 16, a fixed rod 17, and a third fixed plate 18. The first motor 19 and the screw rod 191, the top ends of the four fixed rods 17 are all sc...
PUM
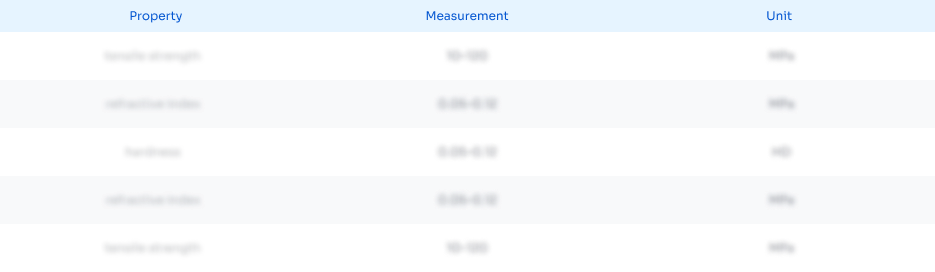
Abstract
Description
Claims
Application Information

- Generate Ideas
- Intellectual Property
- Life Sciences
- Materials
- Tech Scout
- Unparalleled Data Quality
- Higher Quality Content
- 60% Fewer Hallucinations
Browse by: Latest US Patents, China's latest patents, Technical Efficacy Thesaurus, Application Domain, Technology Topic, Popular Technical Reports.
© 2025 PatSnap. All rights reserved.Legal|Privacy policy|Modern Slavery Act Transparency Statement|Sitemap|About US| Contact US: help@patsnap.com