Turbine capable of achieving direct backing and with primary-secondary moving blade structure
A technology of mother blades and moving blades, which is applied to turbines. It can solve the problems of not being able to have normal consistency, low binding capacity of moving blade cascade of reversing turbine, and low efficiency of reversing turbine, etc.
- Summary
- Abstract
- Description
- Claims
- Application Information
AI Technical Summary
Problems solved by technology
Method used
Image
Examples
Embodiment Construction
[0019] The present invention is described in more detail below in conjunction with accompanying drawing example:
[0020] combine Figure 1-5 , the present invention is made up of reversing turbine mother blade 1, reversing turbine sub-blade 2 and wheel hub 3, the turbine mother blade 1 and sub-blade 2 are evenly installed between the casing and the hub along the circumferential direction, and the wheel hub 3 is the last stage of the front-wheel turbine. Blade tip connecting ring. After the analysis of the internal flow field according to the actual situation, parameters such as the airfoil shape, angle of attack, leading edge radius, and circumferential position of the sub-blade are adjusted to improve power and efficiency as much as possible. The invention adopts the method of cutting the center arc of the mother blade to obtain the sub-blade, keeps the center arc of the mother blade unchanged, and intercepts the center arc of the second half of the blade from the axial pos...
PUM
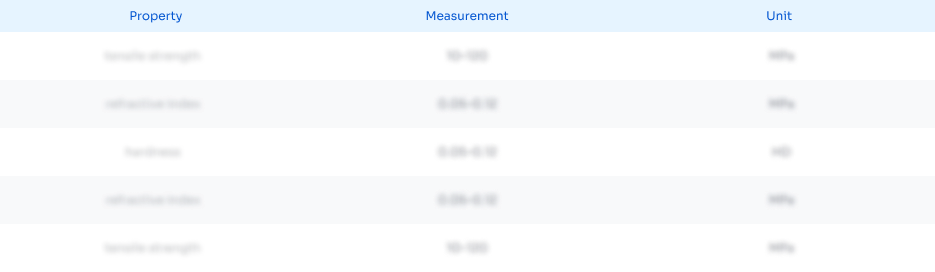
Abstract
Description
Claims
Application Information

- R&D
- Intellectual Property
- Life Sciences
- Materials
- Tech Scout
- Unparalleled Data Quality
- Higher Quality Content
- 60% Fewer Hallucinations
Browse by: Latest US Patents, China's latest patents, Technical Efficacy Thesaurus, Application Domain, Technology Topic, Popular Technical Reports.
© 2025 PatSnap. All rights reserved.Legal|Privacy policy|Modern Slavery Act Transparency Statement|Sitemap|About US| Contact US: help@patsnap.com