Cement final grinding system based on roller press
A roller press and grinding technology, applied in the field of cement final grinding system, can solve the problems of high cost pressure, high particle fineness consistency, low efficiency, etc., and achieve the effects of cost control, quality assurance, and output improvement
- Summary
- Abstract
- Description
- Claims
- Application Information
AI Technical Summary
Problems solved by technology
Method used
Image
Examples
Embodiment Construction
[0019] In order to make the technical means, creative features, goals and effects achieved by the present invention easy to understand, the present invention will be further described below in conjunction with specific embodiments.
[0020] Such as figure 1 As shown, a cement final grinding system based on a roller press, including a roller press 1, a stabilizing bin 2, a V-shaped separator 3, an iron removal device 4, an elevator 5, and a multi-rotor dynamic separator 6 , cyclone dust collector 7, fan 8, dust collector 9 and ball mill 10, the feed inlet of hoist 5 is connected with the belt conveyor from the cement batching station, and the outlet of hoist 5 passes through iron removal device 4 It is connected with the feed port of V-type powder separator 3, the coarse material outlet of V-type powder separator 3 is connected with stable material bin 2, and the fine material outlet of V-type powder separator 3 is connected with multi-rotor dynamic powder separator 6, stable ...
PUM
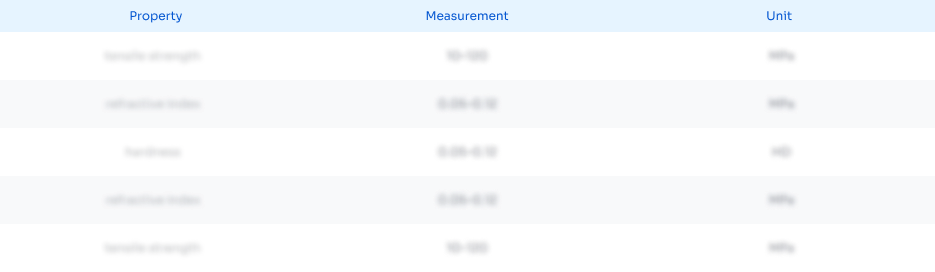
Abstract
Description
Claims
Application Information

- Generate Ideas
- Intellectual Property
- Life Sciences
- Materials
- Tech Scout
- Unparalleled Data Quality
- Higher Quality Content
- 60% Fewer Hallucinations
Browse by: Latest US Patents, China's latest patents, Technical Efficacy Thesaurus, Application Domain, Technology Topic, Popular Technical Reports.
© 2025 PatSnap. All rights reserved.Legal|Privacy policy|Modern Slavery Act Transparency Statement|Sitemap|About US| Contact US: help@patsnap.com