Local thickening method for paper pulp molded product and system thereof
A technology of pulp molding and products, which is applied in the direction of textiles and papermaking, etc., can solve the problems of restricting the shape of pulp molding products, reducing production efficiency, and difficult forming of omentum, and achieves long service life, improved production efficiency, and smooth surface beautiful effect
- Summary
- Abstract
- Description
- Claims
- Application Information
AI Technical Summary
Problems solved by technology
Method used
Image
Examples
Embodiment 1
[0037] The invention provides a process and method for making pulp molded spoon tableware with variable wall thickness. The specific process method used is as follows:
[0038] Step 1: Design the shape of the spoon and get the 3D model of the spoon. The edge contour of the spoon needs to be on the same level when designing, see figure 1 .
[0039] Step 2: Use the Simulation plug-in of Solidworks software to perform stress analysis on the spoon model obtained in Step 1. When holding a spoon, the second half of the spoon handle is the position where the fingers are held, and the spoon head is the position where the load is applied downward when the food is contained. The force analysis results obtained from this can be found in figure 2 .
[0040] Step 3: Use the Grasshopper plug-in of Rhino software to make a 3D model of the wire mesh, see image 3 . The wire diameter of the wire mesh is 0.15 mm. According to the stress distribution diagram obtained in step 2, the area c...
PUM
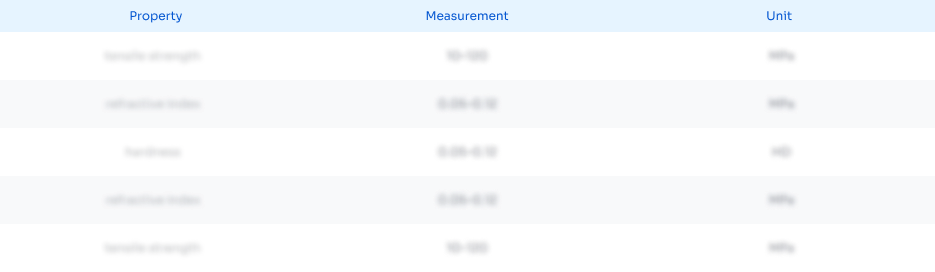
Abstract
Description
Claims
Application Information

- R&D
- Intellectual Property
- Life Sciences
- Materials
- Tech Scout
- Unparalleled Data Quality
- Higher Quality Content
- 60% Fewer Hallucinations
Browse by: Latest US Patents, China's latest patents, Technical Efficacy Thesaurus, Application Domain, Technology Topic, Popular Technical Reports.
© 2025 PatSnap. All rights reserved.Legal|Privacy policy|Modern Slavery Act Transparency Statement|Sitemap|About US| Contact US: help@patsnap.com