Numerical control machining system for die
A processing system and mold technology, applied in metal processing equipment, metal processing machinery parts, manufacturing tools, etc., can solve the problems of large size error, poor surface continuity, and lack of precision of the mold surface, so as to reduce wear and avoid movement Unsmooth, increased precision effect
- Summary
- Abstract
- Description
- Claims
- Application Information
AI Technical Summary
Problems solved by technology
Method used
Image
Examples
Embodiment approach
[0038] As an embodiment of the present invention, the upper surface of the second fixing plate 12 is provided with a second chute 35 on the peripheral side of each rotating rod 13; the cross section of the second chute 35 is hemispherical; The lower surface of each ring 1802 is provided with a third chute 36; a plurality of steel balls 6 evenly arranged are slidably connected in the third chute 36; the second chute 35 corresponds to the third chute 36 set up.
[0039] During work, when the blade 32 cuts the mould, the ring 1802 rotates with the rotating rod 13, and the steel ball 6 slides in the second chute 35, so as to prevent the lower end of the ring 1802 from directly contacting the second fixed plate 12. The fixed plate 12 and the ring 1802 are worn out, and the ring 1802 and the blade 32 rotate with the rotating rod 13 at the same time. A plurality of steel balls 6 make the ring 1802 rotate more smoothly, so that the blade 32 can cut more smoothly. The material of the ...
specific Embodiment approach
[0048] When working, the material of the mold to be manufactured is fixed in the bolt hole 5 on the shell 1 by bolts, and the sample of the mold is fixed in the bolt hole 5 on the lower surface of the die-casting plate 3 by bolts, and the drive is controlled by the controller after fixing The cylinder 4 and the motor 33 work to drive the extended end of the cylinder 4 to control the downward movement of the die-casting plate 3, so that the sample piece squeezes the tip of the rotating rod 13. At this time, the first driven gear 14 moves downward with the rotating rod 13, The first driven gear 14 squeezes the first spring 16 so that the first spring 16 is compressed, and because the first driven gear 14 is meshed with the driving gear 34, the first driven gear 14 keeps rotating, so that the rotating rod 13 is in the second position. The bottom of the first bearing 15 rotates, the rotating rod 13 above the first bearing 15 does not rotate, and the first driven gear 14 twists the ...
PUM
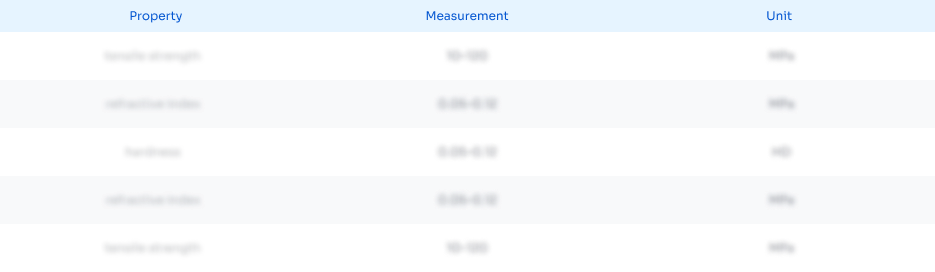
Abstract
Description
Claims
Application Information

- R&D
- Intellectual Property
- Life Sciences
- Materials
- Tech Scout
- Unparalleled Data Quality
- Higher Quality Content
- 60% Fewer Hallucinations
Browse by: Latest US Patents, China's latest patents, Technical Efficacy Thesaurus, Application Domain, Technology Topic, Popular Technical Reports.
© 2025 PatSnap. All rights reserved.Legal|Privacy policy|Modern Slavery Act Transparency Statement|Sitemap|About US| Contact US: help@patsnap.com