AGV-based automatic carrying system and multi-AGV cooperation method
A handling system and automatic technology, applied in the direction of transportation and packaging, conveyor control devices, conveyor objects, etc., can solve the problems of troublesome and troublesome, unable to realize multi-AGV fast cooperative transportation, etc., to improve the use effect, fast positioning and fixing, The effect of increasing friction
- Summary
- Abstract
- Description
- Claims
- Application Information
AI Technical Summary
Problems solved by technology
Method used
Image
Examples
Embodiment Construction
[0046] The following will clearly and completely describe the technical solutions in the embodiments of the present invention with reference to the accompanying drawings in the embodiments of the present invention. Obviously, the described embodiments are only some, not all, embodiments of the present invention. Based on the embodiments of the present invention, all other embodiments obtained by persons of ordinary skill in the art without creative efforts fall within the protection scope of the present invention.
[0047] see Figure 1-9 , the present invention provides a technical solution: an AGV-based automatic handling system and multi-AGV cooperation method, including an AGV trolley 1, an extrusion assembly 3, a moving track 5, a track seat 6, a trigger assembly 10, a cleaning assembly 11, a vibration Component 13, drive assembly 14 and transmission assembly 15, the top of the track seat 6 is fixedly installed with a moving track 5, on which the AGV trolley 1 is slidably...
PUM
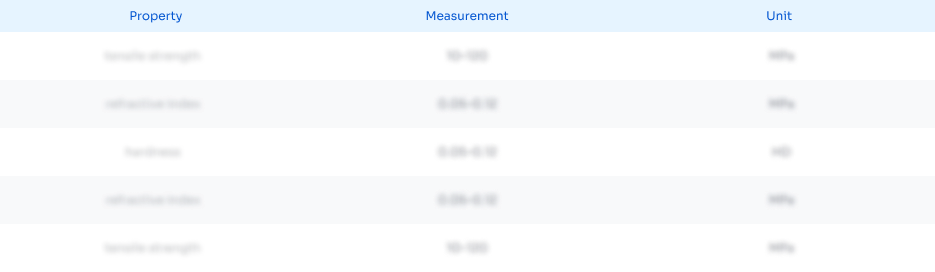
Abstract
Description
Claims
Application Information

- R&D
- Intellectual Property
- Life Sciences
- Materials
- Tech Scout
- Unparalleled Data Quality
- Higher Quality Content
- 60% Fewer Hallucinations
Browse by: Latest US Patents, China's latest patents, Technical Efficacy Thesaurus, Application Domain, Technology Topic, Popular Technical Reports.
© 2025 PatSnap. All rights reserved.Legal|Privacy policy|Modern Slavery Act Transparency Statement|Sitemap|About US| Contact US: help@patsnap.com